Global Site
Displaying present location in the site.
Industrie 4.0 and the Latest Trends in Monozukuri Innovation in the Auto Industry
Vol.10, No.1 December 2015, Special Issue on Enterprise Solutions to Support a Safe, Secure and Comfortable LifeA number of years ago, the German government launched a project called Industrie 4.0, whose goal was to promote a cyber-physical system that would make possible "smart" factories. Likewise, in the Japanese manufacturing industry - where piecemeal improvements have already been implemented - a more cohesive effort is now underway to achieve "Process innovation" through the utilization of Internet of Things (IoT) and standardization of device interfaces. In the meantime, the Japanese auto industry, which is Japan's dominant industry, is undergoing significant structural changes as a result of global production shifts. This paper discusses NEC's proposal for advanced quality management system models based on IoT and big data, as well as related issues pertinent to the achievement of smart factories.
1. Introduction
A few years ago, the German government launched Industrie 4.0, a high-tech project involving industry, academia, and government which promotes the computerization of manufacturing.
In Japan, on the other hand, no national strategy exists, but Japanese manufacturers have been independently pursuing efforts to convert their factories into smart factories. That trend has begun to accelerate as more and more companies realize that continued competitiveness requires them to upgrade their production systems by utilizing the Internet of Things (IoT) to connect factories and facilities and by standardizing factory automation (FA) equipment.
In this paper, we will focus on the structural changes that this environment has stimulated in the auto industry. We will propose a model aimed at making quality management systems more advanced through the utilization of leading-edge technologies such as IoT and big data. We will also examine the issues related to utilizing these technologies to make the production process more advanced.
2. Differences between German and Japanese Efforts towards the Achievement of Smart Factories
Industrie 4.0 is an action plan announced by the German government in 2011. It's a concept for next-generation manufacturers, in which they will be able to create new values and new business models that have not existed before by collaborating with "things" and services inside and outside factories while making the most of IoT and FA.
Now, let's look back at the evolution process from the first to fourth industrial revolutions. Whereas automation took place in the third industrial revolution, Industrie 4.0 aims at the achievement of smart factories that are even further evolved, As such, it is considered the fourth industrial revolution.
- First industrial revolution
Mechanization of industry through use of steam engines - Second industrial revolution
Beginning of mass production through use of electric power - Third industrial revolution
Automation through use of PLC, which combines electricity and IT - Fourth industrial revolution
Achievement of smart factories proposed by Germany
The German government is implementing multiple policies for industry-academia-government collaboration to achieve Industrie 4.0. One of the areas where research is being actively pursued is "plug and produce."
Plug and produce is a concept in which multiple devices made by different manufacturers are autonomously connected and disconnected to and from the backbone cyber-network to enable production to flexibly handle orders in real time. The concept is similar to "plug and play," which was introduced with Windows 95 to automatically set up peripheral devices when connected to the PC to provide a convenient, ready-touse environment.
This concept has also been highlighted by the "It's OWL" project, a collaboration among companies, universities, and scientific centers of excellence. Winner of the German government's Excellence Cluster Competition - a key aspect of its Industrie 4.0 strategy, it's OWL received a government grant amounting to 200 million euros, a fact that makes it clear the importance of this concept to Industrie 4.0.
Furthermore, Germany believes that taking leadership in setting the technological standards of the future is the key to the success of Industrie 4.0. As there is no doubt that optimization control will be executed by combining different devices and software, the importance of standardization of interfaces should be obvious.
Many Japanese manufacturers already use sensors and networks to analyze and monitor production processes and operating conditions in their facilities. By feeding back the results obtained by processing the data collected from computers, they are attempting to convert their factories into smart factories. Table below shows excerpts from publicized case studies.
Table Case studies of innovation aimed towards achieving smart factories in the Japanese manufacturing industry.
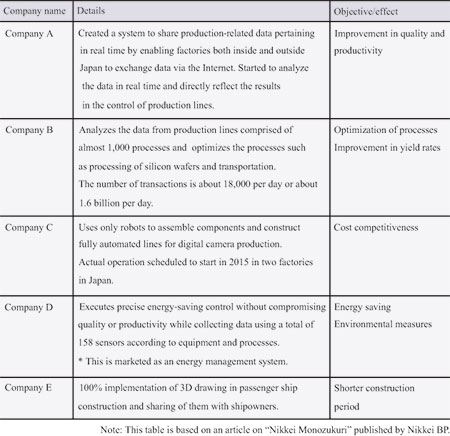
For example, Company A, which is an electronics component maker, connects Japan and multiple overseas factories via the Internet to collect and analyze production and quality data at their facilities. Based on the feedback from these results, they claim that they have achieved optimum production. By analyzing data collected not just from a single factory but data aggregated from multiple factories, their goal is to fine-tune quality control and production management to achieve maximum precision. It is also important to note that the ability to have real-time knowledge of overseas production and quality conditions while in Japan could streamline management of global production.
Similarly, in other cases, it is obvious that many companies are targeting process optimization, increased cost competitiveness, and energy saving.
Now, let's look at the standardization of interfaces in Japan. The Japan Society for the Promotion of Machine Industry standardized an interface for FA equipment called ORiN (Open Resource interface for the Network) and is implementing its adoption and validation tests. The society reported that connecting FA equipment incorporating this interface and control software resulted in a significant reduction in the number of processes required for optimal control of management systems.
Based on what we've seen, it's safe to say that Japan and Germany are heading in roughly the same direction. However, the backing of the German government for a coordinated national strategy may have put Germany ahead of Japan.
3. The Rapid Increase in Global Production and Importance of Quality Management
This chapter discusses the structural changes in the Japanese auto industry - relevant to the trend towards smart factories - and examines the issues in monozukuri* processes caused by those changes.
Fig. 1 shows the transition in the ratios of production volume for Toyota by region on a global scale. The percentage of production volume in Japan was about 62% in 2002, but was down to about 40% by 2012. As there was little fluctuation in the ratios of production volume in regions other than Asia, it is clear that about one third of Toyota's production has shifted to Asia.
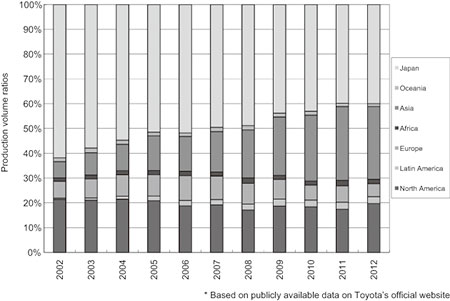
When the ratio of overseas production volume increases, the number of contracted suppliers and the number of managed components increases as well. In addition to obvious issues such as overseas technology transfer, this also leads to an in crease in language and communication problems that can occur in an environment where there is no mutual unspoken consensus at work. This in turn leads to an exponential increase in the complexity of technology management and supply chain management.
Under pressure from the market to reduce development lead time and cost, Japanese automakers have been forced to find ways to streamline the manufacturing process. Typical measures include product architecture innovation using standardized platforms, as well as modularized designing. This methodology is very effective at increasing development efficiency; nevertheless, once a defect occurs in a module or component, there is always the potential risk for a worldwide recall. In other words, it is necessary to strengthen design quality while reforming product architecture.
The auto industry is built on a hierarchical structure that comprises many inter-company supply chains. Their final products - completed cars - are therefore composed of modules and components developed and manufactured by many different suppliers. For this reason, if a defect occurs, the range of investigation is not limited to the company's production processes but also extends to its component suppliers overseas as well as in Japan. In situations where the cause cannot be accurately located or identified, there is a serious risk of massive losses generated by the need to totally replace all suspicious components, as well as potential damage to the company's social credibility.
To sum up, the importance of upgrading and improving the following processes is increasing every year.
- Design review for modules and components developed and produced by automakers and component suppliers
- Traceability of quality for fast, accurate identification of the cause of a problem when it occurs
- Traceability of design changes to make sure that changes are efficiently applied and managed
- *Japanese word that refers to manufacturing which is in harmony with nature and that adds value to society.
4. Upgrading Quality Management Systems Using IoT and Big Data
To evolve to meet the demands of the changing business environment, automakers and their suppliers have been working to strengthen and enhance their quality management systems. The ISO/TS16949 automotive quality management system standard specifies that documents indicating control plans for quality management (management processes and confirmation methods for the quality and properties of manufacturing processes) should be created and then the plans described in the documents should be executed.
Based on these control plans, automakers manage their manufacturing process quality. However, the reality at many production sites is that quality information is recorded and stored on paper. Creating and storing reports on paper can generate the following problems:
- It takes longer to determine the cause when a quality defect occurs
- Inaccessible quality reports in remote places (overseas factories and facilities)
- Inability to utilize report until the next quality fault occurs
Fig. 2 shows a conceptual diagram of a more sophisticated quality management system to solve these problems. Operating information and manufacturing conditions that are output from facilities as well as quality records and information of products and components with serial numbers can be transferred in real time to the quality database. Using IoT technology, these data is transferred via the standardized interfaces incorporated in measuring instruments, equipment/facilities, and tablets for data entry. The collected quality records can be correlated withserial numbers and manufacturing conditions in the quality database, facilitating quality management.
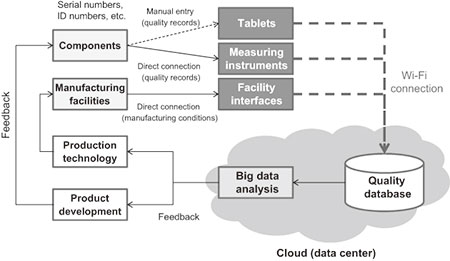
Moreover, the data generated in plants and factories around the world can be integrated at the data center and utilized as big data regardless of its origin.
Once this has been achieved, it should not only enhance quality traceability, it can also be expected to contribute to the overall optimization of facility operating ratios without regard to physical location as well as the prediction of equipment failure and maintenance timing, spur improvements in electric power demand forecasting and in energy saving, and facilitate the detection of hidden knowledge.
5. Strengthening the Traceability of Technology Information Management and Design Changes
The importance of the strengthening design reviews for modules and components and the traceability of design alteration processes has already been discussed in Chapter 3.
In order to maintain a quality management system, the first requirement is the ability to reliably transmit high-quality technology information to production sites around the world and to record the data transmission history. (Although data generated on the site is collected using IoT and analyzed using big data, it is of no value if there is a problem with the data itself.)
However, the process; distributing large volumes of technology information and design alteration information to production plants around the world, as well as maintaining and managing that data, increases operating loads and generates potential problems on both the distributor side and the receiver side. The control plans, in particular, need to be maintained individually with respect to design changes because they are likely to be localized according to the differences in production facilities and processes.
One way to accurately and efficiently distribute technology information is to employ an integrated management method using a list of components or BOM (bill of materials). Fig. 3 shows a conceptual diagram of the integrated management of technology information using the BOM. In the diagram, relationship among information is specified; information to manage components, 3D models and drawing that specifically define the components, information pertaining to the processes to manufacture the components, and control plans to manage the quality of the processes.
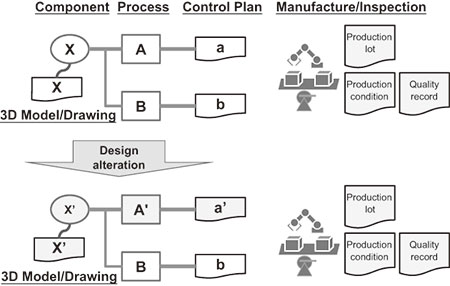
As long as integrated management of technology information is maintained, it will be possible to know immediately that, if 3D Model X or Drawing X that represents Component X is changed, it affects Process A and therefore a change in Control Plan A is required. By tracing the relationship information on the system, you can sift through the items to be changed without missing anything, efficiently performing renewal and distribution processing.
Furthermore, when the design alteration processing is executed on the integrated technology information management system, it is possible to manage the changes before and after the design alteration, the reasons for the alteration, and the traces of the alteration, leading to the strengthening of traceability from a technical viewpoint whenever a quality defect occurs.
6. Conclusion
In the first half of this paper, we discussed the different approaches in the movement towards smart factories in Germany and Japan, while in the second half we looked specifically at efforts to improve and upgrade the capabilities of the auto industry's quality management systems. In terms of strong implementation of a national strategy, Germany would appear to be leading the way. However, there are common aspects such as that the manufacturing industry is playing the main role and that the auto industry is the key industry. So while the strategies may differ, both countries appear to be heading in a similar direction.
It is important to note that the auto industry is an industry in which car manufacturers are supported by a very broad range of supporting players. Regardless of where a company is headquartered, it will have many overseas production plants including in emerging economies, a great number of local employees, and numerous component suppliers from large to medium-and-small companies. All of these contribute to the development and manufacturing process. As it looks to the future, it is essential for the auto industry to take measures that focus on both the horizontal axis (lateral expansion towards globalization) and the vertical axis (mechanisms to support the entirety from large to medium-and-small companies.
The biggest and most basic task for the horizontal axis is the completion of a network and infrastructure environment equipped with the technologies necessary to use IoT, such as Wi-Fi. Some factories still have an inadequate network environment - in some cases not even PCs can be connected, never mind FA equipment. In such cases, the first thing to do when planning construction is to assure a stable Internet connection. Another important task is to take into consideration the durability, dustproofness, and waterproofness of the tablets that will be used. It is necessary to carefully select devices that are suitable for the on-site environment.
As for the vertical axis, a key issue is investment in information systems. Although larger companies can afford to invest in enhancing the sophistication of their production systems, the scale of investment required is difficult for medium-and-small companies to handle on their own. Fig. 4 shows a conceptual diagram of a low-cost, cloud-based service that makes it easy for smaller companies to quickly ramp up the sophistication of their quality management systems.
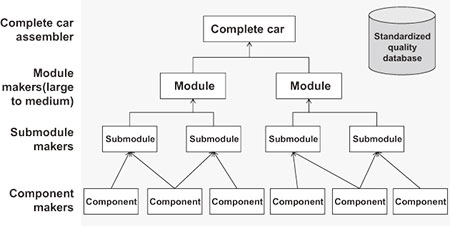
NEC remains committed to developing and deploying services able to contribute to every stratum of the auto industry now and in the future.
- *Windows95 is a registered trademark or trademark of Microsoft Corporation in the U.S. and other countries.
- *Wi-Fi is a registered trademark of Wi-Fi Alliance.
Authors' Profiles
Senior Manager
Consulting Business Division