Global Site
Displaying present location in the site.
Industrial Operations Supporting Industry 4.0
Vol. 11 No. 1, December 2016, Special Issue on AI & Social Value CreationIndustry 4.0 (The fourth industrial revolution) has the purpose of enabling mass-customization in the manufacturing industries and in significantly reducing manufacturing costs by advancing the entire SCM. In the near future this trend is expected to spread throughout the manufacturing plants of Japan. This paper focuses on the industrial operations (operations management) that are applying the AI technology and by which especially important reforms may be expected to be introduced. Industrial operations issues related to cost minimization and quality maximization that are important in applying AI technology are also introduced as are the AI technology procedures used by NEC in this field.
1. Introduction
Industry 4.0 is the name of a manufacturing industry strategic innovation project announced by the German government in 2011. In Japan it is called the fourth industrial revolution. Industry 4.0 attempts to advance the supply chain management (SCM) that covers the entire series of manufacturing industry operations from product design to sales and maintenance in order to enable mass-customization. It also aims to achieve a significant reduction in the manufacturing costs.
In this paper, the authors introduce the orientation adopted by NEC in using its artificial intelligence (AI) technology for the reform and advancement of industrial operations (operations management) at the manufacturing plants.
2. Outline of Industry 4.0, Targets of This Paper
Industry 4.0 aims at implementation of the smart factory based on the cyber physical system (CPS). The CPS collects and analyses information on equipment and people in the real world and aims to control them based on the analysis results. It is a concept that aims at efficiency improvement and optimization of social systems. In manufacturing plants, it has already been put into practice to collect information using sensors and to use such information for the monitoring and control of the manufacturing plants. In the future, advancement of the sensor networks and analyses will result in the factories becoming intelligent and autonomous, i.e. smart factories.
In a smart factory, entire pieces of equipment are networked. The data collected from them is analysed and the results are used as the basis of the concerted control of equipment and persons so as to: 1) minimize the production costs and; 2) maximize the production quality. While all of the existing SCMs are advanced in order to make the above possible, the authors have noticed that the industrial operations (operations management) is expected to offer particularly important innovations by applying AI technology. Below, we will introduce the issues associated with 1) and 2) of industrial operations by forecasting the anticipated situation for around 2020 while defining the approach we will take in making use of our AI technology.
3. Operations Management System for Minimization of Costs
In the future manufacturing plants, unattended operations are expected to increase thanks to the use of big data analysis technology, the AI-based robots and automated control. Although the zero-people operations will minimize the human costs, the robots and production facilities will always be threatened by failures and anomalies in certain circumstances. As the facility availability rate is reduced, which will lead to the generation of the human cost of recovery, the total cost could eventually be increased. In order to prevent this, it is essential to avoid occurrences of failures and anomalies and, even if one should occur, to recover from it at an early stage (Fig. 1).
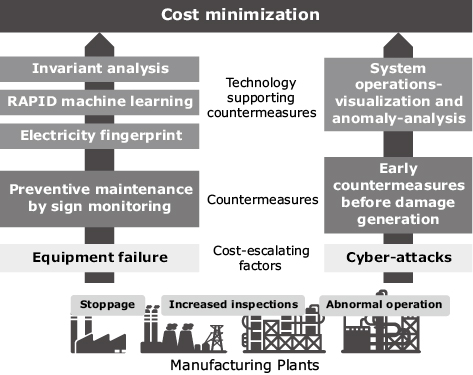
3.1 Cost Escalation from Equipment Failures and Appropriate Countermeasures
In the future, the mainstream means of reducing costs incurred from equipment failures will be to identify a “silent fault” status before a failure occurrence and to adopt pre-emptive maintenance measures. A “Silent fault” refers to the status in which signs of failure are observed before the equipment fails.
NEC is planning to implement pre-emptive maintenance measures by using System Invariant Analysis Technology (SIAT), which detects silent faults with high accuracy (with no false detections) from the invariant relationships (invariants) of the various sensor information and the past fault history. It will thereby be possible to identify the cause of each fault and to suggest suitable countermeasures to be adopted. Moreover, it is expected that utilization of information obtained from sources other than the sensors will contribute to minimizing the number of staff engaged in monitoring and cause identification. We will enable silent fault detection by utilizing media data including video and audio, by means of deep learning applied by RAPID machine learning. The linkage between the sensor information and the numeric data is expected to enable silent fault detection and to thereby provide higher accuracy identification.
Installation of a larger number of sensors will make it possible to know the status of more of the pieces of equipment in detail. However, as the installation of sensors is costly, there is a need, particularly among small-scale enterprises, to attempt to detect the silent faults of equipment without installing sensors. NEC will employ the electricity fingerprint analysis technology1), which acquires the equipment’s current value from the distributor panel and analyses its waveform in order to identify the operating status of each piece of equipment. It will thereby detect silent faults without any additional installation of sensors and will thus identify the causes of faults at an early stage.
3.2 Cost Escalation as a Result of Cyber-attacks and Proposed Countermeasures
In addition to the equipment failures discussed above, it is also expected that the risk associated with cost escalation due to cyber-attacks is likely to increase in the future. As seen in the case of the power plant outages of overseas countries that are probably caused by cyber-attacks2), it is a concern that cyber-attacks on Japanese plants will be occurring frequently by around 2020. It is expected that such attacks will not only be direct ones via the Internet, but will also be caused by virus infections via in-house intranet or by USB memory aids used in maintenance.
As these attacks are becoming diverse and fresh or sub-specific viruses are appearing on a daily basis, the current blacklist-type virus detection using pattern files is regarded as being incapable of dealing with them effectively. To deal with the majority of unknown attacks including those using sub-specific viruses, NEC is conducting R&D into a self-learning anomaly detection technology. This technology builds the normal-status operation model based on machine learning of the operations of the equipment in normal status, detects abnormal status attacks by comparing the current status with the model, and applies early countermeasures before the actual damage occurs. We are planning to advance this technology to enable early detection and apply countermeasures against any kind of attack on manufacturing plants.
For advanced impersonation and spoiling attacks at the network level, network packets for control and wireless LANs in the plants will be monitored to detect impersonations and spoiling attacks and to pre-empt malfunctions caused by such attacks.
4. Operations Management System for Maximization of Quality
Industry 4.0 uses AI technology to support the automation of materials and production quality management (Fig. 2). Thereby the dynamic procurement of raw materials and parts and high quality, low-volume production and mass-customization are secured.
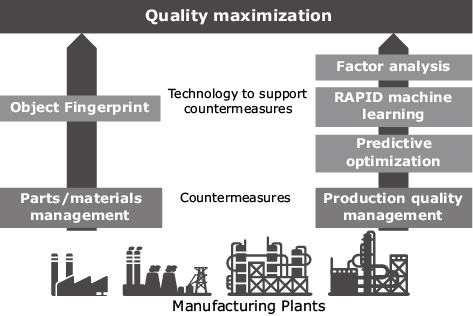
4.1 Parts/Materials Management
Production of diverse quality products requires the consistent quality of the diverse raw materials and parts of every item. Managing where, how and from which materials the individual parts required for assembly are fabricated makes it possible to solve each quality issue quickly by identifying and correcting the time zone, line and raw material that is causing the problem. This applies even when an issue occurs due to a faulty part. NEC employs an object fingerprint technology that can identify individual parts such as screws from the patterns on them and manage the individual part patterns and their attributes (manufacturer, manufacturing date/time, etc.) to enable quality control at the parts level.
4.2 Production Quality Management
Deterioration of product quality or yield may result not only from equipment failure but can be caused by various factors including the environment, raw materials and parts. In order to maximize the quality, it is necessary to detect deterioration of quality soon after it occurs and to correct it as quickly as possible. Naturally, in order to prevent the occurrence of quality deterioration, it is also necessary to adopt pre-emptive measures in advance.
NEC will actively employ RAPID machine learning and SIAT discussed in section 3.1 above as well as the factor analysis3) described herein in order to detect any sign of quality deterioration as early as possible. This procedure will also identify the cause and adopt suitable countermeasures. Additionally, we will also utilize the predictive decision-making optimization technology, which predicts possible future quality deterioration from past data and controls the production system in order to optimize the quality. This strategy helps to achieve automated control and leads to quality improvement.
5. Integrated Monitoring of Production Facilities
Shutdown and quality deterioration of manufacturing plants result from diversified causes including equipment failure, cyber-attacks and operator mistakes. The operator should permanently monitor signs of such issues and in a case in which an anomaly is observed, be required to identify the cause, such as a failure, attack or operator mistake, and adopt the necessary countermeasures quickly.
At present, the monitoring operations are divided, with the operation/maintenance department monitoring the equipment and quality, and the IT department monitoring the security (Fig. 3). In the future, such operation flow should be changed into the “integrated monitoring system”. The operator will, for example, assign monitoring and cause identification to an appropriate department and countermeasures based on the identification results to a specialized department. It should be noted in particular that the first part composed of monitoring and cause identification is to be performed efficiently by a small number of persons and that these persons will also be required to have suitable knowledge and experience.
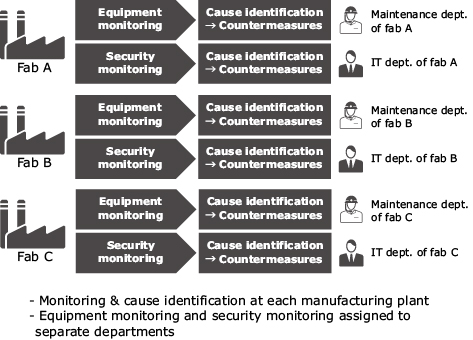
NEC possesses SIAT which links actual cases of equipment/quality fault countermeasures with the results of numerical data analyses and turns the results into usable data. This technology enables identification of the causes of various faults and suggests countermeasures by learning the fault handling records of a specific piece of equipment from our own as well as other manufacturing plants. It may thus model the learning results into useful information so that the required data and experience may be supplemented. With new equipment that has not yet acquired sufficient fault handling records, the procedure enables analysis of unknown causes and presentation of a countermeasure policy based on fusion of the AI and simulation technologies.
We believe that the integrated monitoring of efficient data organization will consist not only of monitoring a single plant but also of the remote monitoring of several manufacturing plants (Fig. 4). Ultimately, enterprises providing monitoring as a service will be established and the monitoring will be outsourced to such enterprises.
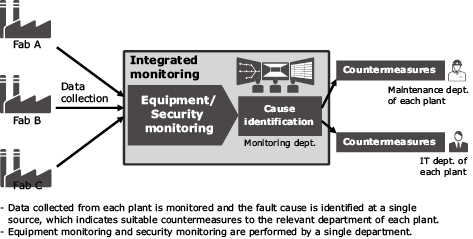
6. Conclusion
In the above, we have described issues of cost minimization and quality maximization in Industry 4.0 era, together with the approach orientation taken by NEC. The basis of this approach is to monitor the production systems and products using sensors, to visualize them, analyse the monitored data and feedback the results to the production system. NEC intends to pursue further R&D by aiming at the early implementation and practical realization of various AI technologies for use in the operations management of its manufacturing plants.
Reference
1) KOUMOTO, et al., “Electricity Fingerprint Analysis Technology for Monitoring Power Consumption and Usage Situations of Multiple Devices by Using One Sensor”, NEC Technical Journal, Vol. 10, No. 2, pp. 96-98, April 2016
3) ASAKURA and OCHIAI, “Quality Control in Manufacturing Plants Using a Factor Analysis Engine”, NEC Technical Journal, Vol. 11, No.1, pp. 58-61, December 2016
Authors’ Profiles
ASAKURA Takayoshi
Senior Manager
Security Research Laboratories