Global Site
Displaying present location in the site.
DX Initiatives in Field Service Management
DX Offerings to Promote Business InnovationAt the construction, operation, and maintenance sites of capital-intensive industries involving infrastructure and plant development, civil engineering, and building construction, aging facilities, information distribution and isolation, as well as manpower shortages are issues. There is an urgent need to improve the efficiency and optimization of field operations through digital transformation (DX). In field service management, it is important to obtain a sense of acceptance from the field staff and align the direction of the digital transformation with that of the DX and the information systems departments to achieve overall optimization. This paper introduces NEC’s approach to this process. As concrete examples of our shared DX offerings and efforts in co-creation with clients, we will introduce digital plants with the aim to realize digital twins for the plant industry as well as initiatives to support in-house development of digital twins through low-code development.
1. Introduction
In recent years, field service management (FSM) at the construction, operation, and maintenance worksites of capital-intensive industries has been facing issues such as aging equipment, information distribution/isolation, and labor shortages. There is an urgent need to improve the efficiency and optimization of on-site operations through digital transformation (DX).
In this paper, we will introduce NEC’s DX offerings to help solve these issues and provide case studies of shared efforts at co-creation with our clients.
2. Challenges in Field Service Management
Construction, operation, and maintenance sites in capital-intensive industries face shared challenges in terms of equipment and people (Fig. 1).
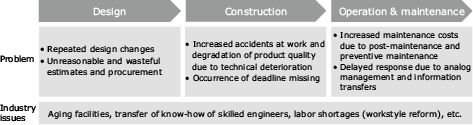
2.1 Equipment: Aging facilities
Much of the equipment in basic infrastructure and plants is aging. Because of a lot of renovation or renewal work, blueprints might not be available or might differ from the current situation, making it difficult to accurately assess the condition of facilities. When formulating a construction plan, it is always necessary to reconfirm (resketch) the site and study the route to take while viewing photographs — this can account for nearly half of the planning work.
2.2 Quality: Decrease in work efficiency and quality due to information distribution and isolation
Although vast infrastructure and plant facilities contain a vast amount of information regarding design, construction, operation, and maintenance, only a limited number of people have a grasp of all this information, and in many cases, information is not shared among teams. Furthermore, this information is distributed and managed across all systems and paper documents, making it difficult to obtain timely information when it is needed. This means that the preliminary preparation for production and maintenance planning must start with a search for information — a task that is said to account for approximately 30% of the total workload.
Even in the case of new construction, information regarding the design, construction, and operations or maintenance is often created and managed separately by each contractor. To efficiently create a high-quality plan for operations and maintenance, it is important to understand the entire life cycle of the facility and to collect and manage the information in an integrated manner.
2.3 Human resources: Labor shortage
In capital-intensive industries, chronic shortages of labor continue because of a declining workforce, the norm of long working hours, and the image of being dirty, dangerous, and difficult (kitanai, kiken, and kitsui or the 3K in Japanese). In particular, compliance with the revised Labor Standards Act will be required as of 2024, and violators will be penalized. As a result, an urgent need exists to improve labor productivity through the full use of information and communication technology (ICT) and to work toward creating workplaces that are more appealing.
3. NEC’s efforts in Field Service Management
These issues are shared by many of the capital–intensive industries, and NEC provides comprehensive support from the planning stage when business issues and measures are examined to systems development and operations to maximize the effects of DX-based on-site business reforms.
NEC has been working on the development of a shared DX offering that involves the departments of field operations and information systems and also on a development process that allows for immediate feedback and improvement of field evaluations. Through shared planning support and agile, flexible development, we will realize the co-creation of DX with a high level of acceptance in the field.
From Section 3.1, as a concrete example of our work with clients, we will introduce NEC’s support service for requirement development in field service management as a consulting-based DX offering that provides planning and requirement development support and formulates solutions for clients — that is to say digital plants — that aim to realize digital twins for the plant industry. We will also introduce NEC’s efforts in the development of digital twins with the aim to support in-house production through low-code development.
3.1 Support service for requirement development in field service management
NEC’s support service for requirement development in field service management is provided to clients such as those in the aforementioned capital-intensive industries, especially those who are unable to incorporate DX strategies and digitalization policies into concrete initiatives and are unable to successfully define the solutions needed to realize DX strategies and digitalization policies. This is a consulting-based DX offering for clients facing challenges so that together we can study and define a system to improve the efficiency and the optimization of on-site and administrative tasks.
NEC personnel who have an understanding of business in this area will work with the clients to identify the root causes of business problems, organize the measures to be taken, and formulate effective requirements for subsequent system development, such as incorporating the measures to be taken into a business/functional overview. This allows us to efficiently define solutions that are directly linked to the realization of the client’s strategy as well as the ability to implement those solutions.
NEC’s support service for requirement development in field service management involves six steps from problem identification to requirements verification and is provided in 105 business days (Fig. 2). This DX offering emphasizes the development of requirements for solutions that are characterized by the FSM domain as being on-site (construction, operation, and maintenance operations) and involves the ability to be implemented. In this shared DX offering, the client’s DX department and also people who are in charge of on-site operations or who have experience in the field are assigned to the project to co-create solutions.
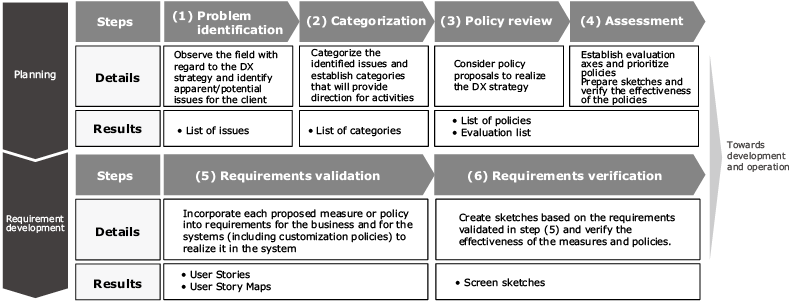
In addition, this DX offering provides a list of issues, measures to take, evaluations, user stories (materials equivalent to use cases of measures that can be taken), user story maps (materials equivalent to functional overviews of measures), and screen sketches. This makes it easy for clients to have a concrete image of the measures that will be taken and enables a smooth transition when clients actually request the development of those measures.
3.2 Digital Plants
A digital plant is a 3D visualization of a plant in virtual space and a reproduction of the plant in real space that is associated with the information on the plant’s equipment, specifications, and people. Currently, the inability to easily access scattered information and systems when on site frequently results in reduced quality and productivity. This problem can be solved by providing timely access to information and systems that are centralized and stored in a digital plant without regard to location for all aspects of plant operations and equipment maintenance.
NEC’s concept of a digital plant is realized through the use of cloud applications, and users use a web browser. The plant in virtual space is represented by point clouds measured by 3D LIDAR, and all related information such as drawing data and maintenance history management systems can be linked to the equipment in the plant.
A chemical manufacturer recently converted part of its plant into a digital plant. We measured the point clouds containing approximately 280 power points, including the main 5-story plant and its periphery, and used dedicated processing software to synthesize all the point cloud data, compress it, and implement it in a cloud environment. In addition to user passwords, user management in this cloud environment is enhanced with two-factor authentication for device security.
As a first step, the client had a first-hand experience of the digital plant by temporarily linking the equipment in virtual space with the document management system in which field drawings and operation manuals are stored. Participants extracted several scenarios from the on-site perspective, such as how this could be used in actual operations or how this could significantly change the work itself.
In the second step, we will work together with clients to examine what truly usable DX should look like in on-site operations, including 1) specific linkage methods with other existing systems, 2) combinations with NEC’s AI technologies such as predictive failure detection using invariant analysis and 3) rust/crack detection technologies using RAPID machine learning, and 4) the transformation of information access using digital plants (Fig. 3).
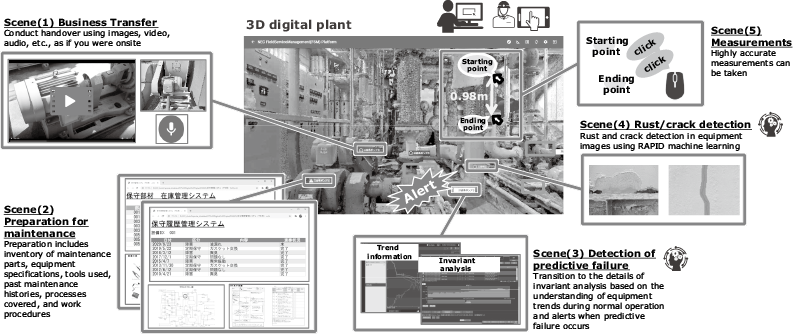
3.3 Initiatives to support in-house development of digital twins
Some of NEC’s clients are attempting to solve the issues described in Section 2 by integrating data that was previously managed separately in each department, each affiliated company, and each process into a single data model and by optimizing business processes from a company-wide perspective. Resolving such issues will result in improving the profitability of the entire company.
In the field of FSM, all the data from drawings, tests/inspections, site record photos, work progress reports, and safety indicators are integrated. In recent years, attempts have been made to map various types of integrated data onto a digital twin to share information and improve communication efficiency by transcending organizational barriers and space and time constraints. For example, there are attempts to use data recorded during on-site inspections at the time of building construction for post-construction maintenance and management.
In addition, some companies have begun in-house development of digital twins optimized for their own business processes. In many cases, even if ready-made products are introduced, they are not used onsite. To immediately respond to onsite requests (and improve employee engagement), the decision is being made to develop in-house and to introduce agile development methods.
In recent years, companies without advanced programming skills have been able to bring in-house ICT systems without outsourcing to IT vendors by introducing a low-code development platform (LCP). A prototype of a digital twin for FSM was developed in a short period of time using LCP, and it was confirmed that in-house development can be done without advanced programming skills as long as the functional blocks for digital twin development are prepared in advance. We also found that when it comes to actual operation, however, assurance of quality, performance, and security is essential, and advanced IT service management skills are required. For example, when rendering 3D data of a building acquired with a 3D scanner on a smartphone, the amount of data processing required for point clouds and polygons is extremely large with heavy battery consumption when using a smartphone (causing the device to get unusually hot) and prevents smooth rendering. We believe that this is an area that can be solved by combining NEC’s technologies in networks (5G, etc.), AI, and cloud systems integrators (SI) to optimize 3D model rendering for smartphones. We will continue to work with our clients to realize this through co-creation.
4. Conclusion
In this report, we have introduced NEC’s DX offerings and specific examples of co-creation with clients to solve on-site work issues in construction, operations, and maintenance in capital-intensive industries involving infrastructure, plants, civil engineering, and architecture. The examples of digital plant initiatives introduced in Section 3 are being exhibited as of March 2022 at the Future Creation Hub, a showroom in NEC’s headquarters (Minato-ku, Tokyo). Through this and other exhibits, we will present a new way of doing on-site work and management in the FSM field. Based on these ideas, we will promote DX to our clients through co-creation with them.
Authors’ Profiles
Assistant Manager
Digital Business Offering Division
Assistant Manager
Digital Business Offering Division
Assistant Manager
Digital Business Offering Division
Assistant Manager
Digital Business Offering Division
Assistant Manager
Digital Business Offering Division