Global Site
Breadcrumb navigation
FlexProcess Production Management uses the unique concept 'Production Model' . As opposed to a Bill of Material for discrete manufacturers, Production Model is specially designed for the process manufacturers (food, chemical, etc.) to accurately reflect their manufacturing process that take s place .
The Production Model is the heart of FlexProcess and can be used to manage production, planning, and costing for process manufacturers, accurately considering real world constraints and conditions.
'Schedule' is used to identify what you plan to produce, how much, when, and how, while the 'Schedule Activity Form' is used to record progress on schedules.
Production Model
The production model includes input (consumed) and output (produced) resources for each process stage, as well as the sequence of processes required for production. FlexProcess can handle process specifics such as co-products, by-products, and recyclables in addition to recipe and yield.
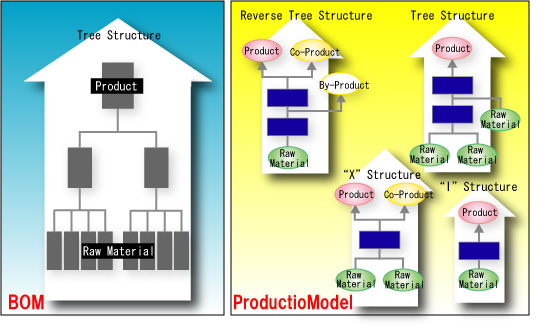
Production Model can handle variations in process structure, such as reverse tree(X), (I) and others as well as the standard tree structure. It perfectly fits in the process manufacturers where multiple outputs (by and co products) are produced at the same time from a single raw material.
You can define multiple Production Models for one product in the following cases:
- Multiple production processes on different equipment
- Multiple recipes with different resources to use
- Multiple recipes for each season
The sequence of resource usage can be specified for each process stage. Each consumption resource on the process stage has the effective date to indicate the earliest and latest date that the resource can be used.
Production Model Examples
Following is a simplified example of the production process for instant coffee.
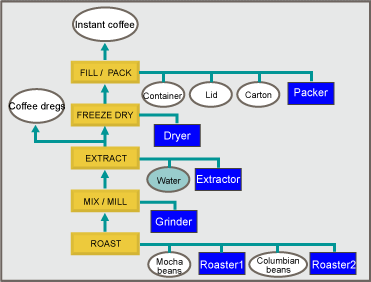
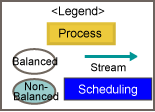
In this example, all the process stages (ROAST, MIX/MILL. EXTRACT, FREEZE DRY, FILL/PACK) required for the finished product is defined in one Production Model. These process stages can be divided into multiple Production Models in regard to how production schedules are released and activities are reported, and where the inventory is produced.
(See the example of division or process stages.)
For each process stage, input and output resources are defined. In the example of ROAST stage, the raw materials (Mocha and Columbian beans) and the roasters are consumed, and the roasted beans are produced as a semi-finished product. It is consumed in the next process stage MIX/MILL. In the extraction process the coffee dregs (leftovers from extraction) are by-produced and become targets of production management.
Production Schedule Management
The Production Schedule is created by defining the Production Model to schedule, the quantity, and the date of production. The Schedule contains all the information needed for production, including consumed and produced resources, machinery used, and resource quantity requirements.
Schedule activities such as consumption/production quantities and lots, can be recorded to update schedules as well as inventory. You can report multiple lots for one resource, and add Reason Codes for specific transactions such as losses.
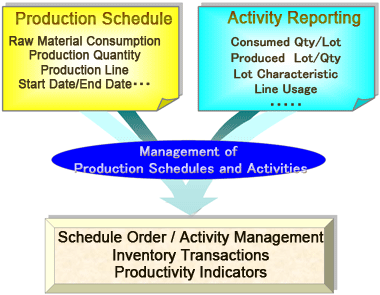
- Record activities against production schedule.
- Inventories are consumed / produced.
- Compare the Planned schedule and its reported activities to analyze the productivity.
Contact