Global Site
Displaying present location in the site.
Column
Review this part of your product development process!
Ideal system of product information sharing platform for product development in global
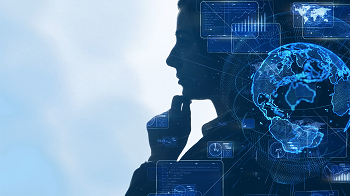
Many companies are trying to increase their sales and profits in emerging countries which have become huge market. However, Chinese, South Korean and Western companies have already expanded their business in the emerging countries, and it would be difficult for any company to emerge as a winner in this market, unless they do not have the product development process that can continuously produce new products which meet the local needs. This time, NEC would like to explain the direction of “Product Information Sharing Platform for Global product development” while clarifying challenges of product development process.
Challenges of product development process
1)Difficult to have collaborative development beyond organizational barriers.
⇒ As a result, the timing of launching new products to the market gets delayed and gaining sufficient market share becomes difficult which leads to decrease in sales. 2)Code system, forms and business processes are different for each manufacturing site and business. ⇒ As a result, it obstructs the early start-up of new business and reorganization of business corresponding to the changes in the market. 3)Concept of product gets changed during the product development process. ⇒ As a result, if the concept of new product that meets the local needs is not properly reflected, the product will be different from the intended product at the time of shipment.
Realizing collaborative development and engineering beyond the organizational barriers
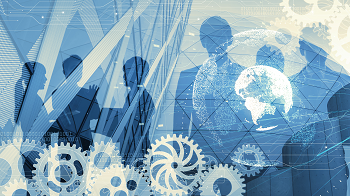
Since most of the companies in manufacturing industries have hierarchically organizations, therefore it is difficult for them to have collaborative development beyond organizational barriers (In actual there are very few companies which produce remarkable results beyond organizational barriers because of decision making abilities of charismatic managers present in these companies). As a result, the development period gets prolonged, the time to launch new products to the market gets delayed, and sufficient market share cannot be gained, which would cause loss in sales.
In the product development process, information shared and communicated between departments includes BOM (Bill of Materials) in addition to engineering deliverables such as drawings (2D and 3D), specifications.
In manufacturing, BOM is commonly used across the product development process as master information and hence it is vital for collaborative development.
However, BOM is managed separately according to the purpose and use of application for each process and department. It can be said that this is the biggest factor that has obstructed the collaborative development.
A typical example for the difference between engineering BOM and a manufacturing BOM. The engineering department creates a BOM focusing on the function and structure, whereas the manufacturing department rearranges the BOM according to the inventory control and ordering. Under these circumstances when an engineering change occurs, it becomes very difficult to reflect the changes done at the engineering BOM side to the manufacturing BOM side without any mistake and in a timely manner.
In order to resolve these problems, the BOM by each application are centrally managed in a database with multiple tables (E-BOM, M-BOM, etc) and the relationship between multiple BOMs such as E-BOM and M-BOM are maintained in a common system with Integrated BOM management. This way one can understand quickly and accurately the level of impact at the time of engineering changes and can also communicate the contents of such changes accurately when changes are required.
It can be said that this process is the key to matching information related to manufacturing with things. Furthermore, it is considered that the key process is the linkage of information between engineering and manufacturing in the realization of the cyber-physical system (digital twin),
Many companies have systematized the individual process such as engineering manufacturing, procurement and have also promoted the digitalization of information. In IT system and data linkage beyond such organizational barriers, the information linkage (adjustment of information) operation is carried out manually to maintain the consistency of information, is this not the case?