Global Site
Breadcrumb navigation
Combining Safety and Efficiency in Transport Robots
Risk-Sensitive Stochastic Control Technology
Featured Technologies January 27, 2022
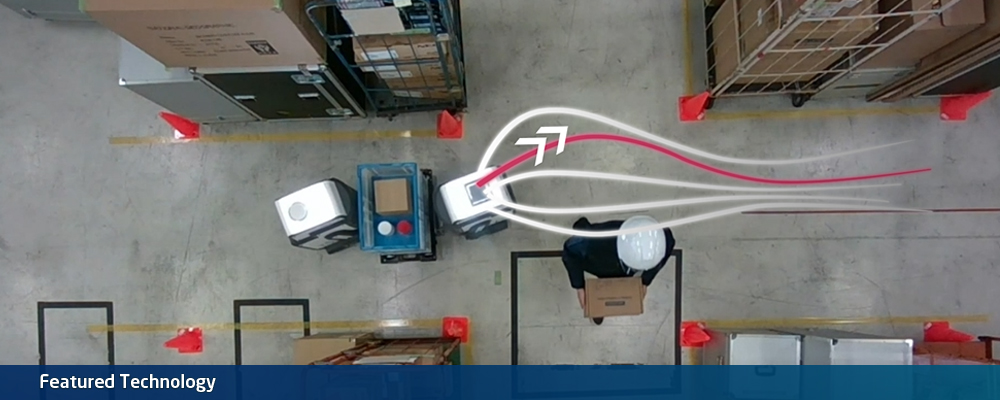
The recent jump in logistics volumes and drop in the working population over the last several years has pushed the logistics industry to improve the efficiency of its operations. Against this backdrop, NEC has announced a risk-sensitive stochastic control technology that can be used for transport robots in warehouses. We interviewed a researcher to learn more about this technology for achieving a high level of both safety and efficiency.
Doubling Throughput While Maintaining Safety
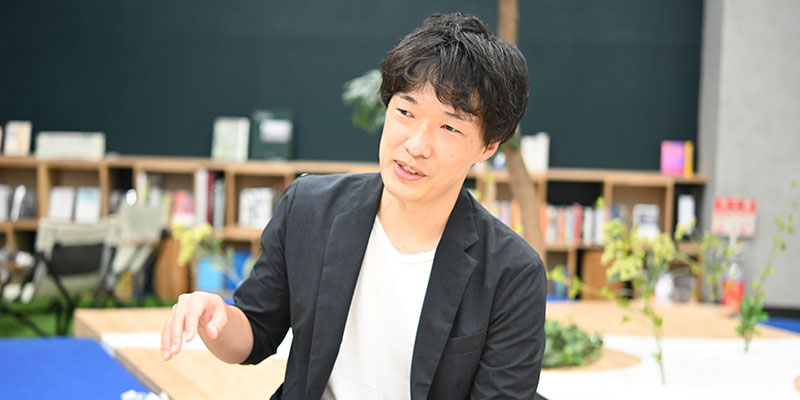
Senior Principal Researcher
Hiroshi Yoshida
― What kind of technology is a risk-sensitive stochastic control technology?
Yoshida: This is a technology that can enable a high level of both safety and efficiency in robot control. For example, in the case of the AGVs (Automatic Guided Vehicles) that we are developing for use in warehouses, ensuring safety by preventing contact with people and objects is a prerequisite for introducing the robot in the front line. However, if the AGV is too slow or pauses too many times to ensure safety, its efficiency will decrease and it will be useless as a robot. Since logistics warehouses are in a harsh work environment where profits are based on the number of units transported per hour, the pursuit of throughput is also extremely important. risk-sensitive stochastic control was developed as a technology that is useful for this type of situation. Compared to conventional AGVs, AGVs equipped with this technology can almost double their average speed without compromising safety. This means that the efficiency is approximately doubled.
On the other hand, the speed can be slowed on hazardous narrow roads for avoiding collisions. In our experiments, the conventional AGV collided with the surrounding wall 9 out of 10 times, while the AGV equipped with the new technology was able to pass through a narrow road with sharp turns without hitting the wall even once. This is why we feel that this technology will enable high-level avoidance of collisions and contact with surrounding people and objects. The cost for adopting this technology can be kept low because there is no need to prepare a dedicated transport path for the robot.
In fact, the technology itself, risk-sensitive stochastic control, has been around for some time. It has been used in the world of mathematical finance. Since the risk of "bankruptcy" should be absolutely avoided in asset management, it has been used as a means to maximize profits while avoiding high-risk investments. The key point of our current research and development is that we were able to apply this technology to the field of real-time robot control and implement it as a technology that maximizes efficiency while avoiding the worst risk of "collision."
In addition to my expertise in mechanics and robotics, Dr. Yasuda, who had been working on quantum statistical mechanics, was in charge of the software, and Mr. Kumagai, who is an expert on networks, was in charge of robot implementation and hardware. I believe that this technology was developed by each of us drawing from our unique fields of expertise.
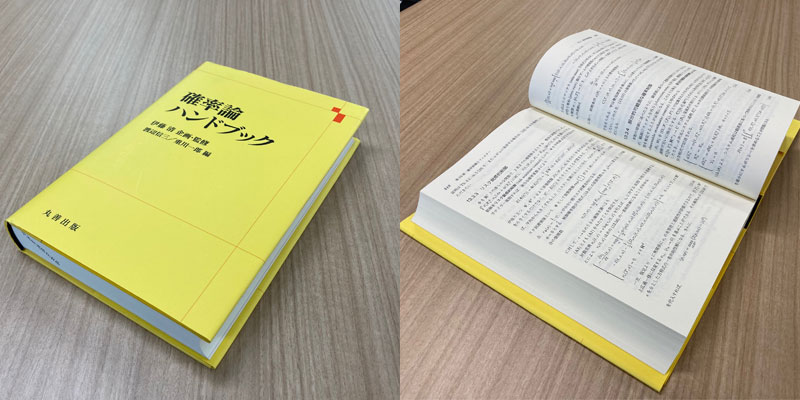
Instantly Calculating the Results of Multiple Patterns of Predictions and Selecting the Best Course of Action
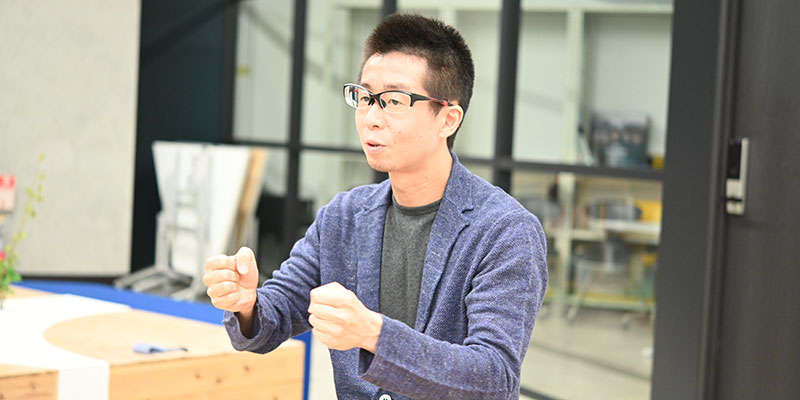
Senior Researcher
Taichi Kumagai
― Why is the performance difference about twice that of conventional models?
Yasuda: Conventional AGVs mainly used differential equations to determine the control input. However, differential equations have only one solution. It is possible that the control input could be high risk. Besides, in real-world robot control, there are many unstable variables. For example, there are errors in measurement, errors in sensors, and errors in control power. In order to deal with these real-world instabilities, this new technology adds an element of stochastic variation to the differential equations. Since this stochastic differential equation has a different solution each time it is solved, we can assume various behaviors by the robot. In this process, we conduct risk assessment for each and every future behavior of the robot to select the best control input. The risk-sensitive evaluation function, which is the core of this technology, serves as the basis for risk assessment at a particular time. It assigns poor risks to obstacle collision in its evaluation, and as a result, it avoids excessive risks for ensuring stable operation.
Also, the risks that this technology avoids are not limited to safety factors such as collision and contact. Factors related to efficiency, such as deviation from a route and extended operation times, will also be evaluated as risks. This is why we are able to achieve both a high level of safety and efficiency while taking into account the risks involved in both. While assessing these various factors, the system automatically makes decisions such as increasing the speed in low-risk situations and decreasing the speed in high-risk situations, and controls them in real time.
Adaptive Remote Control Enables Complex Processing in Real Time
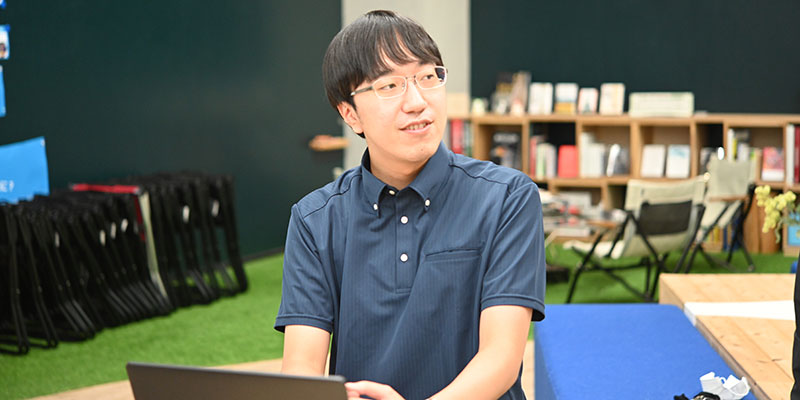
Senior Researcher
Shinya Yasuda
― Aren't considerable computational resources required to perform higher-order processing in real time?
Kumagai: It is true that risk-sensitive stochastic control is a considerably processing-heavy technology. However, we didn't have to worry about that because this technology is based on the adaptive remote control that we developed earlier Normally, sensors and computers are installed in the machine body to control such robots, but in the solution using adaptive remote control, the robot is sensed by cameras mounted to the ceiling, and the computational process is done by a computer in the control room. There are no sensors or high-performance CPUs in the robot. This frees the robot from problems such as power consumption and computational resources, so that even heavy computational processes such as risk-sensitive stochastic control can be used freely.
In particular, NEC's AGVs use a unique method of collaborative transport where two AGVs sandwich the target in order to be able to handle a wide range of cage trolleys at different sites. Because we are running two vehicles, we must be extremely cautious about control errors. Since the development of adaptive remote control, we have been upgrading the hardware to provide more power and speed, and so this technology, which further enhances the safety, is already an element with an exceptional track record. A great synergy between hardware and software has been created.
― What are your plans for the future?
Yoshida: First of all, we would like to take the AGV that we are currently developing and turn it into a viable product. This technology can also be applied in a wide range of environments where safety and efficiency are required. We would like to continue our research while considering applications to forklifts, which have many similarities with AGVs, and to construction machinery such as hydraulic excavators.
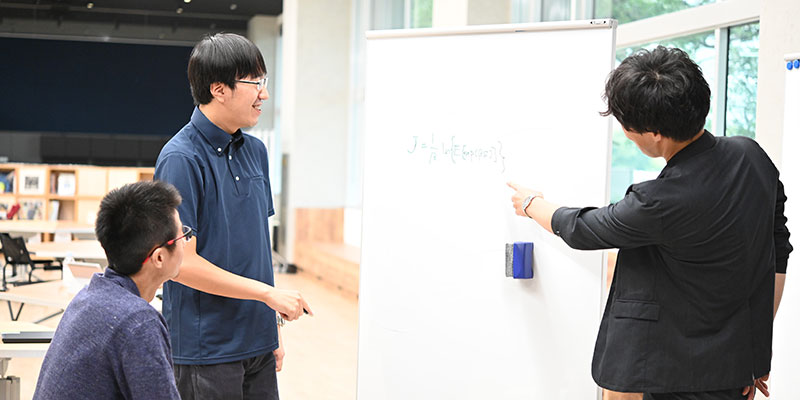
- ※The information posted on this page is the information at the time of publication.