Global Site
Breadcrumb navigation
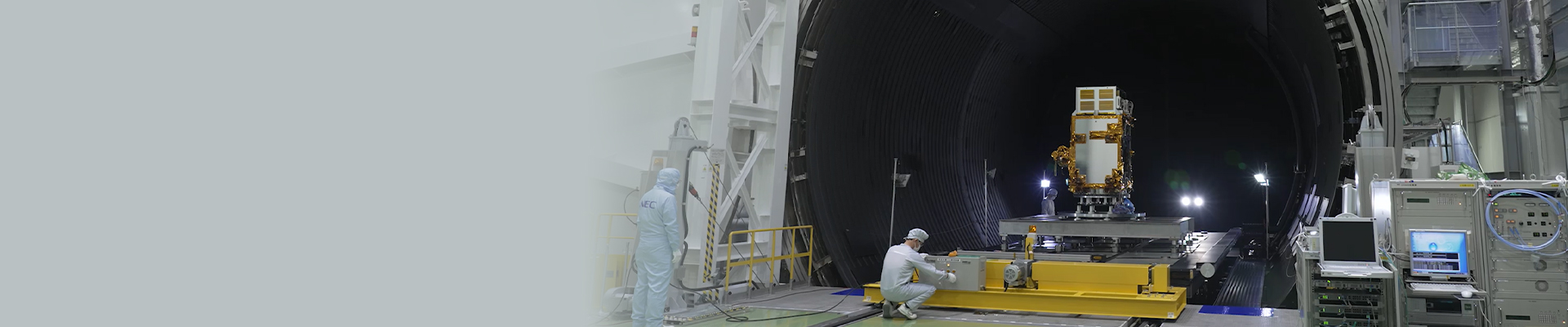
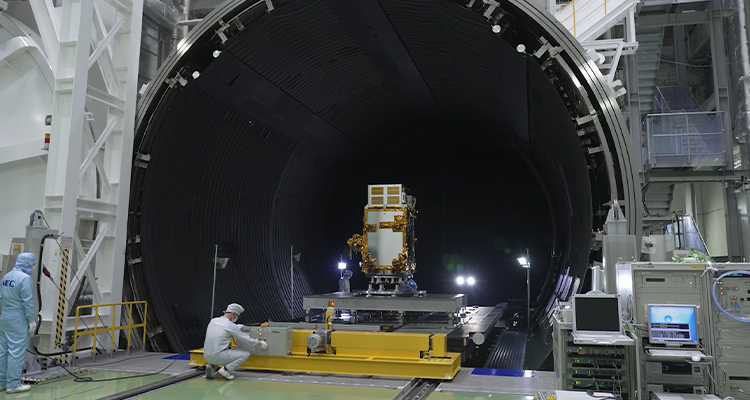
Vibrations during launch, supersonic shocks, and harsh thermal environments…What tests must satellites pass to complete a space mission?
The equipment onboard satellites is manufactured in compliance with the stringent standards (JERG*) set forth by the Japan Aerospace Exploration Agency (JAXA). Only equipment that has passed vibration, shock, and other tests can be integrated into satellites. At NEC’s Satellite Integration Center, where satellite assembly takes place, numerous verification tests simulating the space environment and launch are performed on completed satellites. It is only once a satellite has passed these tests that it can be launched. We sat down with six members responsible for such tests—from those performed on satellites themselves to the equipment and parts comprising them.
*JERG: JAXA Engineering Requirement Guideline. Technical standards for satellite development managed and published by the Japan Aerospace Exploration Agency (JAXA).
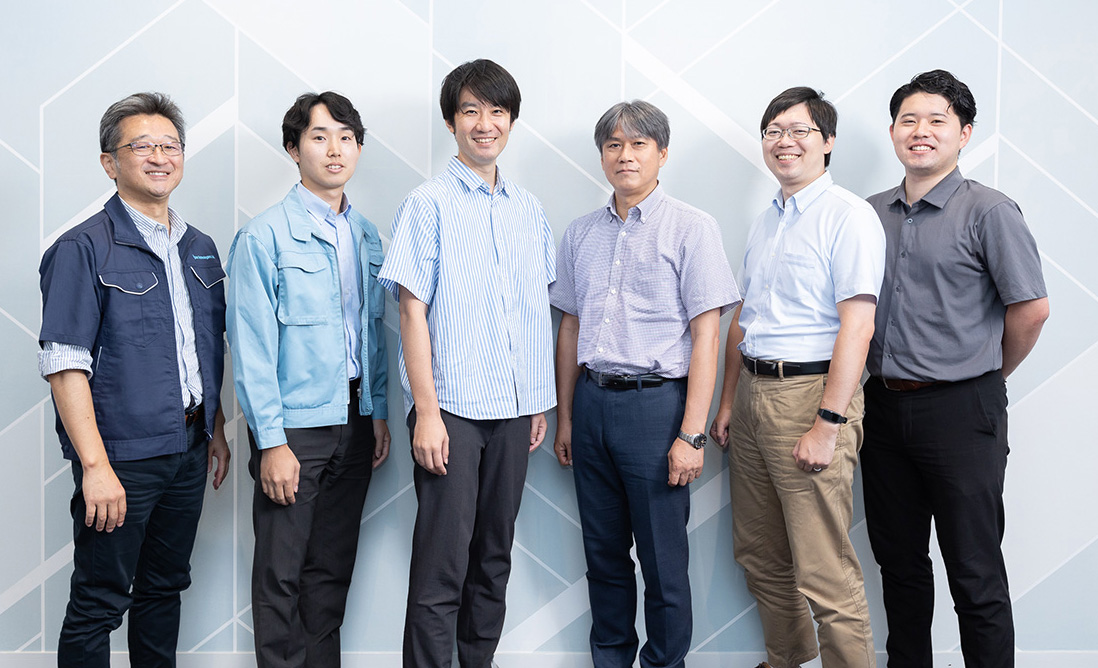
Developing various test environments suitable for satellite systems and onboard equipment
──Please tell us about your background and your current job.
Hirasawa: After joining NEC in 1992 and spending 10 years engaged in a different line of work, I was transferred to the Aerospace Business Division. I am now primarily involved in the coordination of testing for satellite systems, launch site work plans, and initial post-launch operations.
Hozumi: I have been in charge of satellite structural design since joining NEC in 2014. Satellites are exposed to a variety of environments from the time they are manufactured to the completion of their mission, including heavy loads at the time of launch and temperature fluctuations while in orbit. My job is to design the satellite to maintain its configuration and ensure that the installed equipment is supported with the prescribed accuracy even when exposed to such environments. Up until now, I have been responsible for the structural design of subsystems such as solar array paddles* and optical inter-satellite communication equipment as well as the mechanical system design and structural design of satellite and spacecraft systems. In addition, I have been tasked with mechanical environment testing, which is part of the design verification process.
*Solar array paddles convert solar light into electric power and supply the satellite with this power. These paddles remain stowed at the time of the launch and are deployed when the satellite detaches from the rocket.
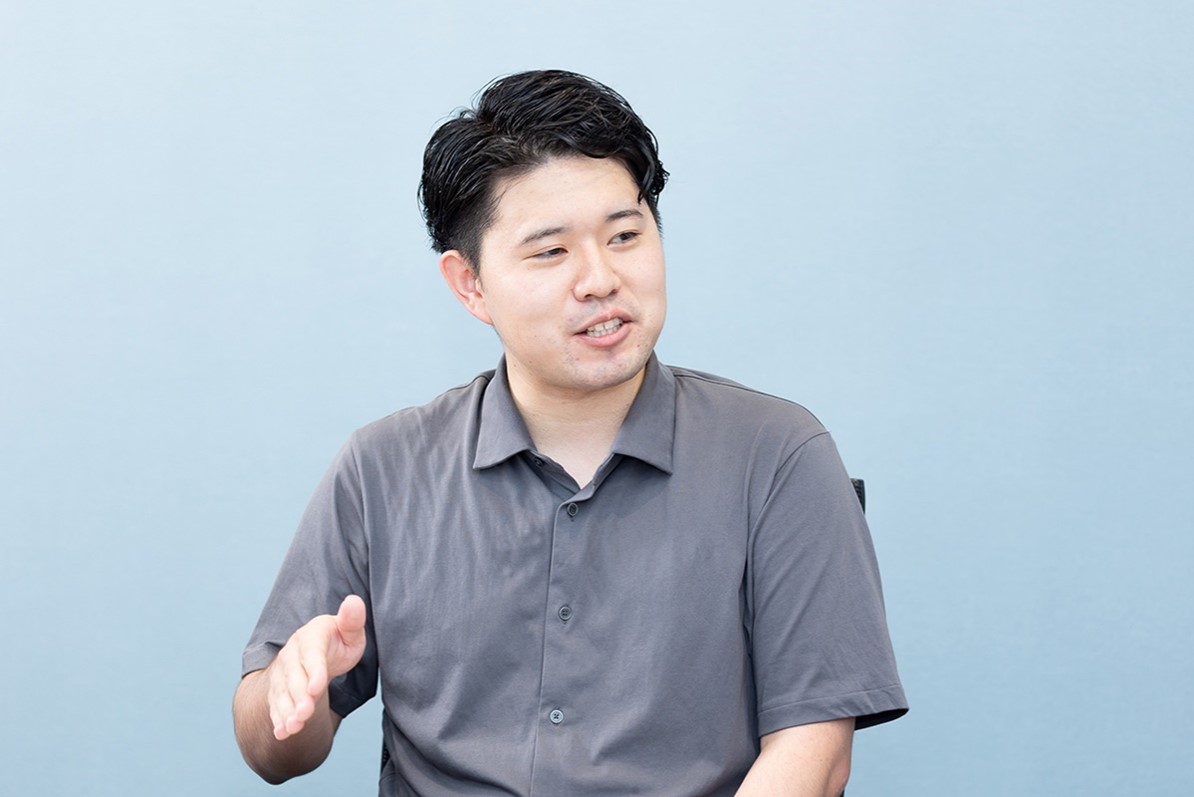
Okada: I joined NEC in 2020 when I was fresh out of university, and am currently responsible for the thermal design of satellite systems in the same department as Hozomi. To complete missions in the harsh thermal environment of space, which fluctuates between -200°C and 200°C, the cooling and warming of the satellite must be controlled so that it can function properly at any temperature. Our mission is to consistently perform thermal control and thermal testing.
Furukawa: After joining NEC in 2009, I spent about ten years engaged in the structural design of satellites as an engineer, working on everything from design to analysis, assembly, and testing. Then, in 2019, I was seconded to NEC Corporation of America for three years. While there, I was involved in the procurement of satellite equipment from U.S. companies and carried out research on the U.S. space market and technology trends. Upon returning to Japan, I started working on developing and promoting new technological strategies such as the digitization of satellite development and the application of AI to satellite testing.
Sugawara: I joined NEC in 1992, was seconded to NEC Space Technologies in 2001, and have since then been involved in the manufacture of radio frequency (RF) equipment used for communications and radar. Up until now, I have been primarily responsible for power regulation and testing work, and I am currently in charge of managing production for the RF group. Since I have been building and promoting hardware for testing automation from early on, I had the honor of being selected for the 2019 Minister of Education, Culture, Sports, Science and Technology Prize for Creativity and the NEC Group’s Outstanding Technical Skill Award. In 2024, I also became an NEC Certified Space Meister.
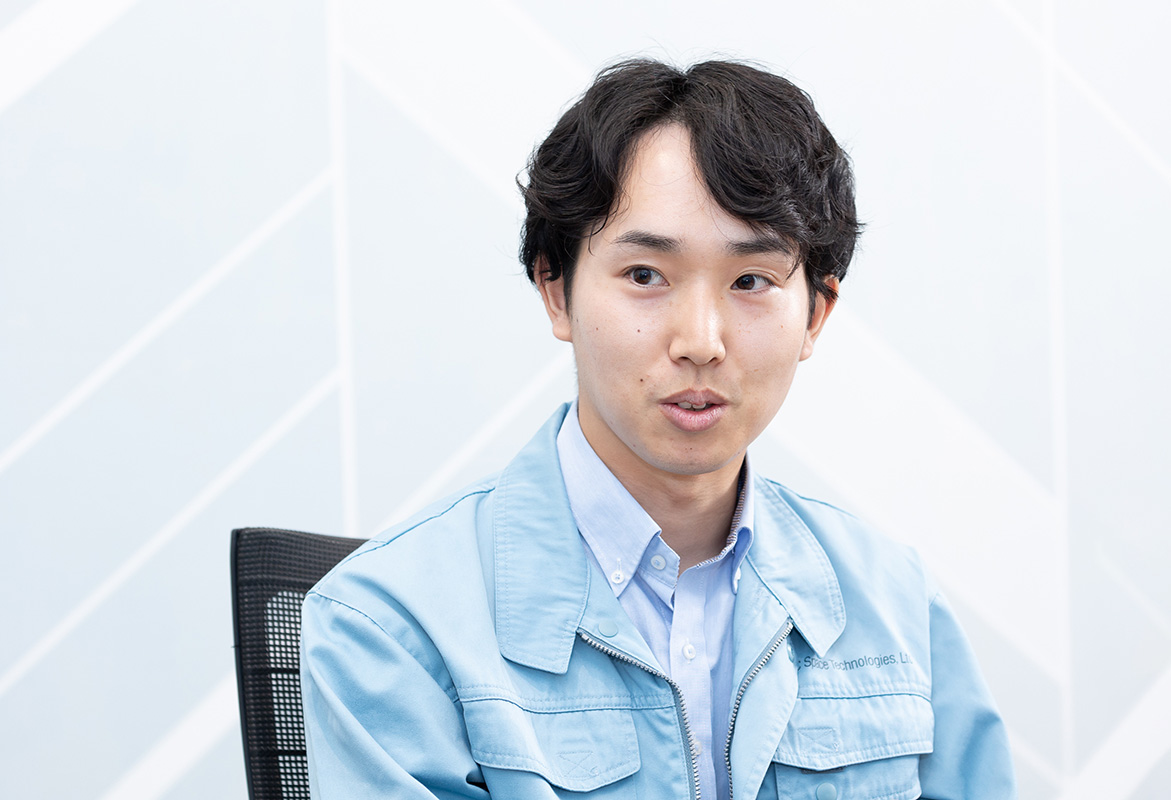
Hoshino: I joined NEC Space Technologies in 2013 and am in charge of the inspection and testing of RF and satellite communications equipment. In recognition of my efforts to automate electric power regulation and testing, which is considered extremely challenging, I was nominated for the NEC Group Technical Skill Incentive Award in 2023. Currently, I am striving to hone my inspection skills as a candidate for “Associate Master” certification, which was established in FY2024.
──Please tell us about the testing environment at NEC Space Technologies.
Sugawara: We perform environmental and electrical tests on devices and parts that will be installed in satellites. While these are small in scale compared to satellite systems, there are countless types of inspections to be carried out and an overwhelming number of devices to be tested, which means it is always a race against time. That’s why our entire company is rapidly moving toward automation. In the case of RF equipment, we have created an environment enabling efficient verification using software developed in-house.
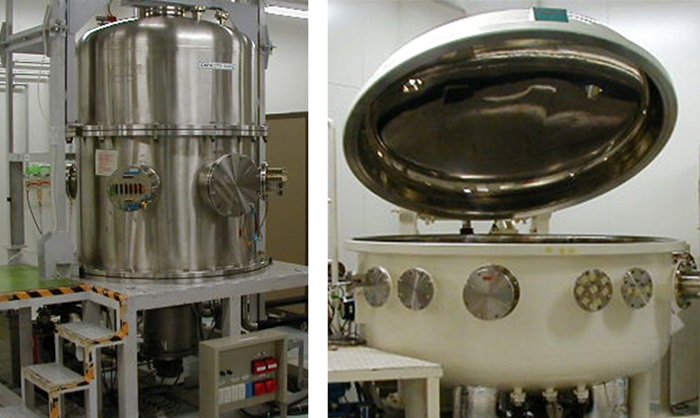
──Various satellite tests are performed at the NEC Group’s Satellite Integration Center. What kind of equipment does the Center have?
Hirasawa: The Satellite Integration Center is a facility built on the premises of the NEC Fuchu Plant where satellites are assembled and tested. This facility features a large space chamber and a clean room measuring more than 20 meters high. It also has the equipment to conduct acoustic, vibration, alignment, and mass property tests. But what truly sets it apart is that all the tests necessary to launch a satellite can be performed in-house.
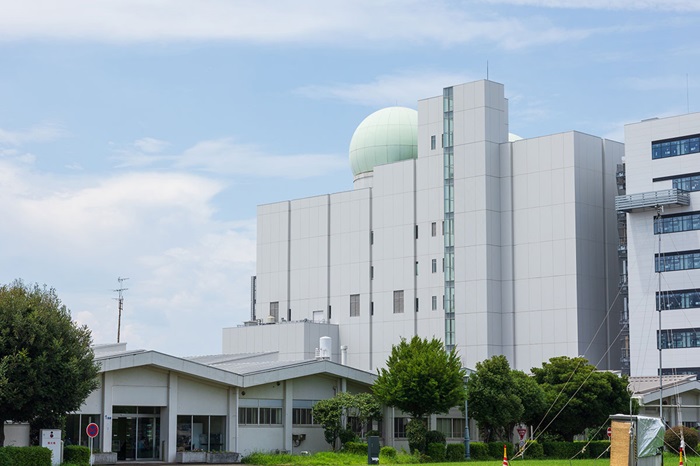
Satellite testing in a harsh environment simulating space and efforts to automate analysis
──Could you please tell us about the tests performed at the Satellite Integration Center?
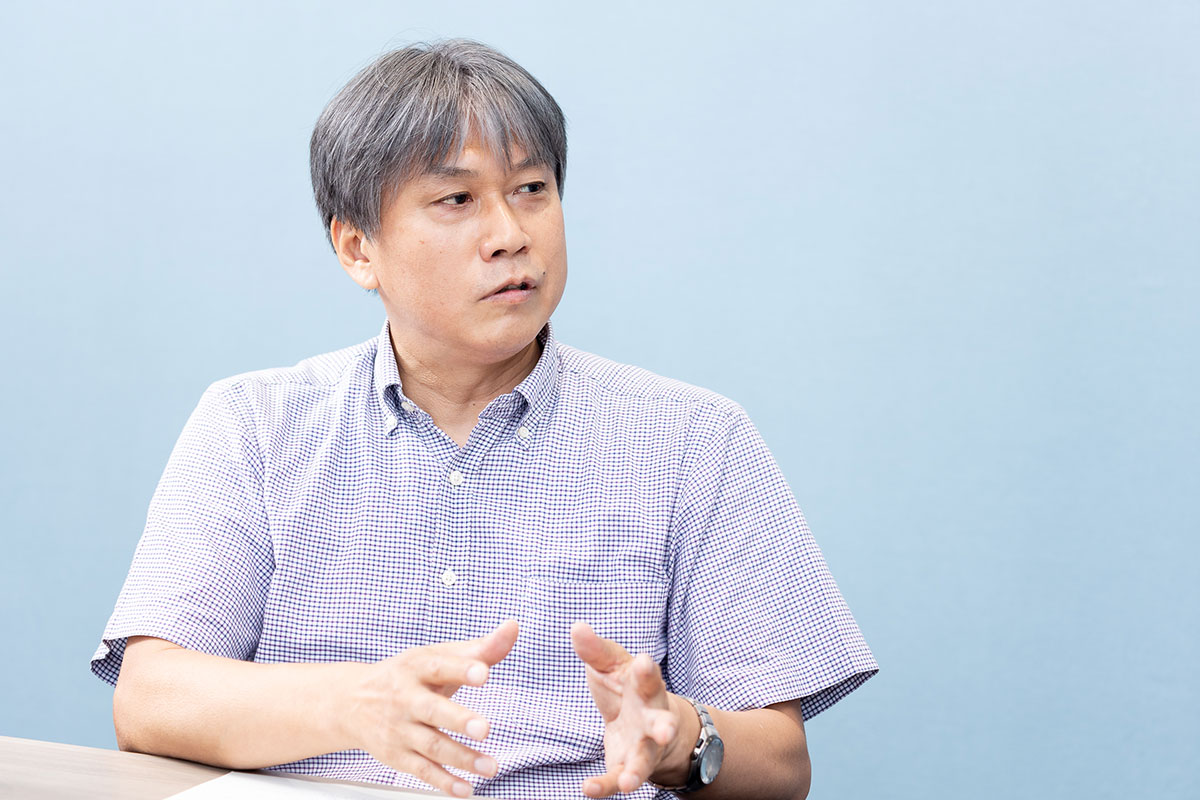
Hirasawa: At the Center, we perform testing in an environment simulating outer space and launch conditions. These tests can be grouped into four major categories: thermal vacuum testing, vibration testing, acoustic testing, and shock testing.
Okada: Thermal vacuum tests are carried out in an airtight vessel called a chamber. The inner walls of the vacuum chamber are cooled with liquid nitrogen to simulate temperature conditions in outer space, and the satellite is heated with a heater to simulate orbital heat input. The aim of these thermal vacuum tests is to evaluate the validity of the analytical model and the functional performance of the satellite and its onboard equipment by exposing it to a high and low temperature environment created in this way.
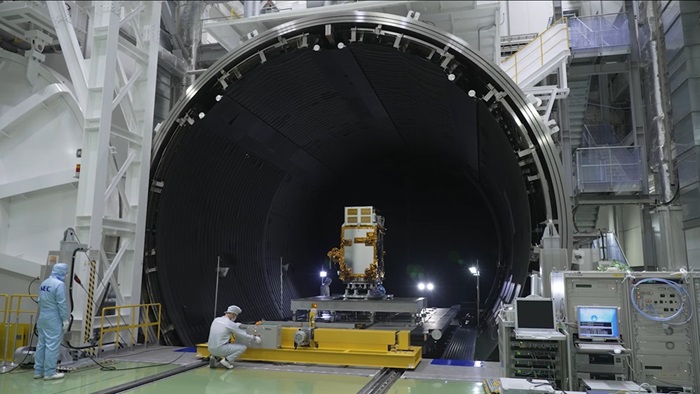
Hozumi: While thermal vacuum tests are performed in an environment simulating space, vibration, acoustic, and shock tests are conducted with the launch in mind. In vibration tests, the satellite is placed on a vibration table and subjected to horizontal and vertical vibrations to determine whether it can withstand the vibrations that occur during launches. Depending on the part, large vibrations ranging from 10G to 20G are generated. Acoustic tests verify whether the satellite can endure the sound environment created by the acoustics during rocket launch or fluid vibrations during rocket flight within the fairing (the cover that protects the satellite from air pressure and frictional heat during launch).
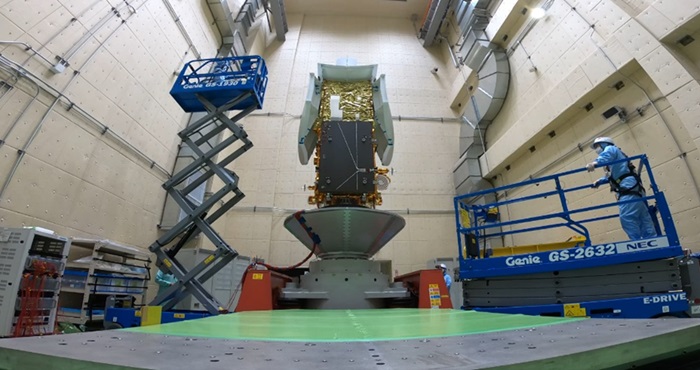
──What kind of environment is created for acoustic testing?
Hozumi: Acoustic tests are conducted in an "echo chamber" to reproduce the aforementioned sound environment as a diffuse sound field. During the test, we generate sounds as loud as 130 dB or 140 dB, which are unbearable for humans, so the echo chamber is equipped with a double door composed of a 2-meter-thick heavy-duty door and a shutter.
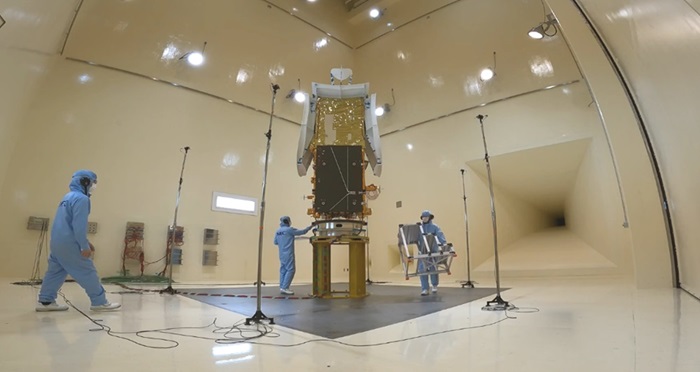
──Could you also explain the shock test?
Hozumi: The shock test simulates the impact when the satellite is separated from the rocket in space, or the shock caused by the release of deployable structures like the solar array paddles. We often use separation mechanisms and hold-release mechanisms* that are equivalent to the actual systems for these tests.
*A hold-release mechanism combines a retention mechanism that maintains the retracted state during launch and a release mechanism that deploys after the satellite detaches from the rocket.
──How are the parts and equipment mounted on the satellite tested?
Hoshino: NEC Space Technologies conducts comprehensive tests on individual devices and boards. We evaluate the voltage and signal output performance and communication frequency stability based on the state of the boards and hybrid integrated circuits (HIC). We also test various performance aspects after assembling them into equipment.

Sugawara: Adjusting high-frequency signals entails not just observing the waveform with measuring instruments. Since precise tasks such as soldering and bonding are also involved, testers must possess skills equivalent to those of the manufacturers. The automation of the testing system, however, enables sharing adjustment results via the system, allowing personnel from different departments to check the data immediately from their desks. This is, in fact, one of the strengths of NEC Space Technologies.
Hoshino: RF equipment uses a wide variety of measuring instruments, so learning how to operate them is quite challenging. Automation, however, has made it possible to substantially reduce both testing and operational errors. We are also working on improving and automating devices that have not yet been automated by making proactive proposals from the field.
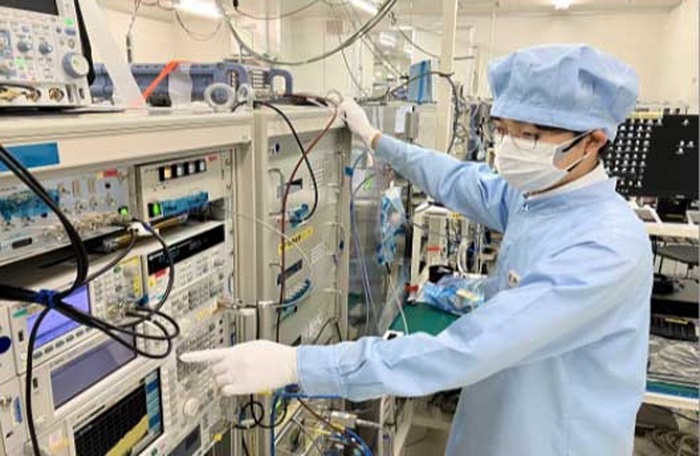
──It seems that you have started using AI in initiatives to automate satellite system testing.
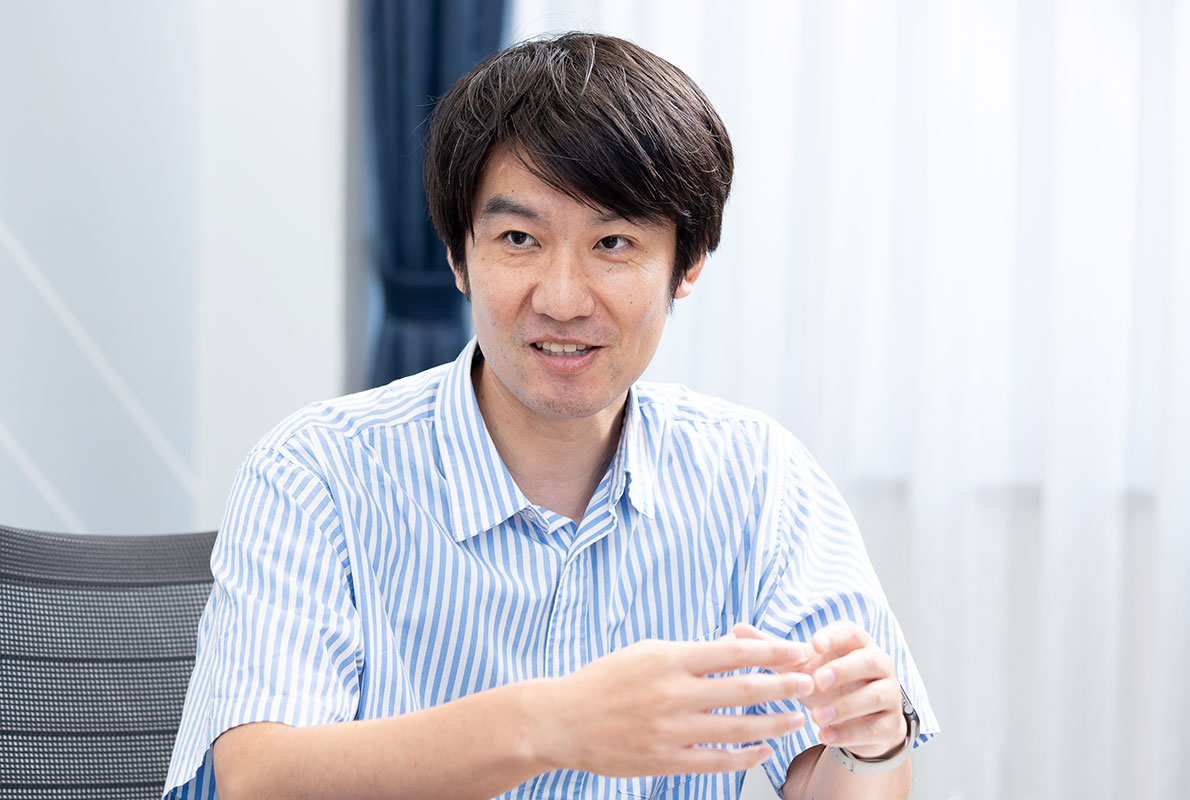
Furukawa: Yes. We are carrying out a project utilizing NEC's proprietary AI engine called "invariant analysis," which enables early anomaly detection, fault location identification, and diagnosis. This technology was adopted in spacecraft development at Lockheed Martin in the U.S. in 2017 and has been highly evaluated. We are now working to integrate these results into NEC’s own satellite development and testing. Together with the Biometrics & Vision AI Department and NEC Solution Innovators, we are currently building a data analysis platform equipped with invariant analysis. I am in charge of overseeing this project.
──How much efficiency does invariant analysis bring to testing?
Furukawa: Previously, when a problem occurred, we had to manually verify each piece of data one by one, so it took a lot of time to identify the cause. With invariant analysis, it is possible to instantly detect anomalies from a large amount of data and pinpoint the problematic areas. This allows us to shorten the process of identifying the cause, which used to take 30 days, to just three days.
The NEC Group strives to reach the goal as one team
──Please tell us about the challenges, rewards, and key points in your daily work.
Okada: Thermal vacuum testing runs continuously day and night, taking about 1 to 2 weeks for equipment and subsystems, and about a month for system-level testing. It involves a never-ending cycle of trial and error, but the sense of accomplishment upon passing the test is immense. Also, when I hear the news that the satellite I worked on has been successfully launched, I feel truly happy, which motivates me to press on.
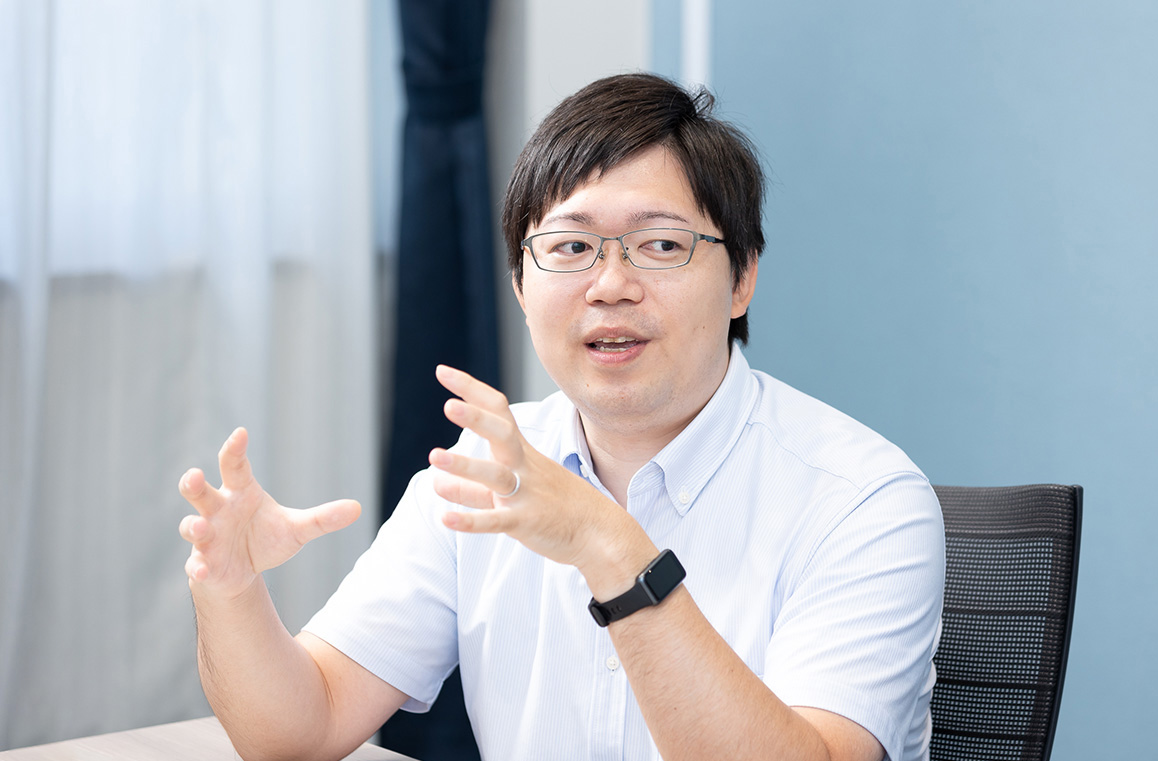
Hozumi: All mechanical environment tests are difficult, but vibration testing is especially challenging. Unlike shock or acoustic tests, the environment itself cannot be fully replicated, so we must gradually increase the vibration levels to ensure the satellite does not get damaged by excessive internal responses that would not actually occur during the launch. To set the testing levels, we gather a huge amount of data for each test, which must be evaluated in a short period of time. Right now, I am working with Furukawa and others to create a system that can efficiently collect and analyze these data.
Furukawa: When I tackle new things, I make it a point to discard all preconceptions. Rather than giving up because “I have never been done it before,” I believe it is important to simply ask, “Why can it not be done?” or “How can it be done?”
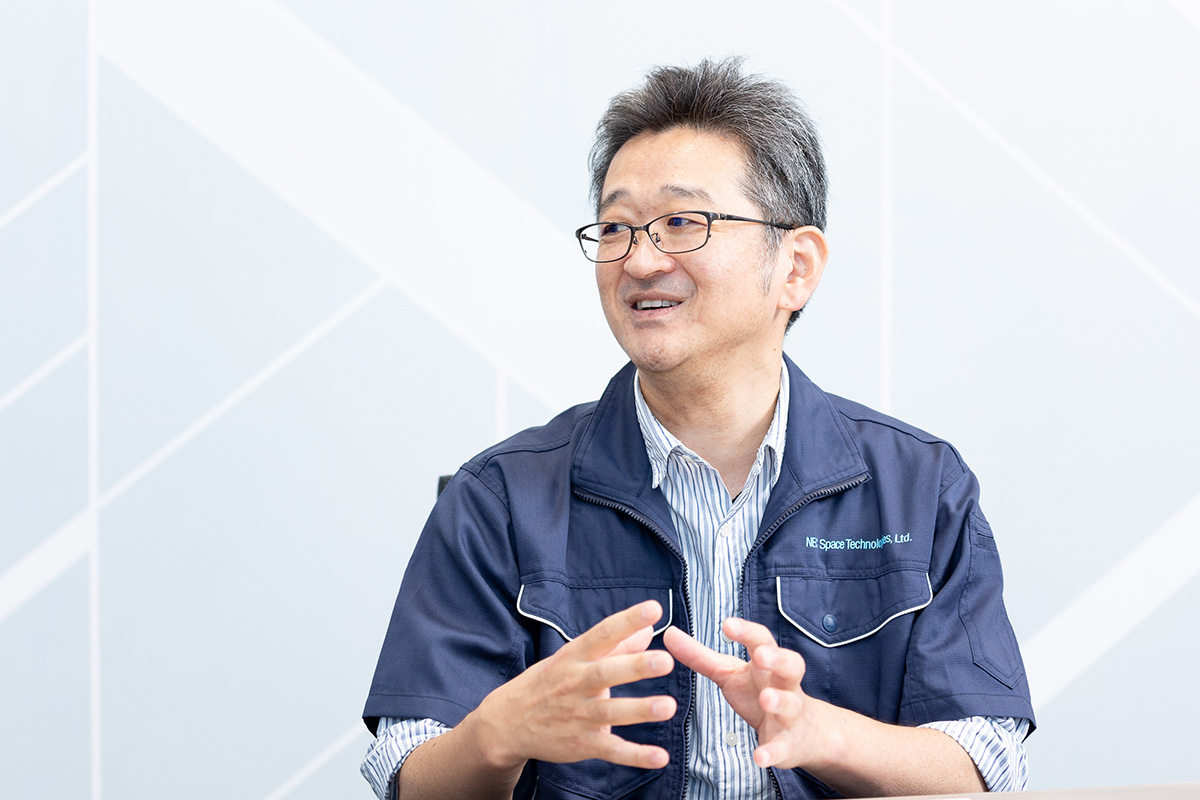
Sugawara: The automation of tests requires the understanding of those you work with. I have made various efforts in this regard, but it did not always proceed as smoothly as I had hoped, and I had to overcome a lot of challenges. However, once people are on board, they give their full support, which is what makes our team members truly reliable. With the help of strong advocates, automation has progressed rapidly after a certain point. Even though we work for different companies, the fact that we can work as one team toward the same goal is a huge advantage of the NEC Group.
Creating new value with satellites
──What kind of value do you think your work brings to society?
Hozumi: The Purpose of the NEC Group is to “create the social values of safety, security, fairness to realize a sustainable society.” I believe that disaster monitoring and weather observation using satellites directly contribute to achieving these social values, primarily safety and security.
Okada: NEC not only designs, manufactures, tests, and operates satellite systems, but also excels at analyzing and utilizing the data obtained from satellites. I think the NEC Group’s strength lies in its ability to not only build satellites, but also leverage them to create the next value. I want to continue working with various departments to contribute to society.
Hoshino: Just as seeing Japanese athletes succeed on the global stage motivates us to keep going, I believe the successful launch or mission of a "Made in Japan" satellite can inspire the entire nation. I think that is one of the values our work brings to society.
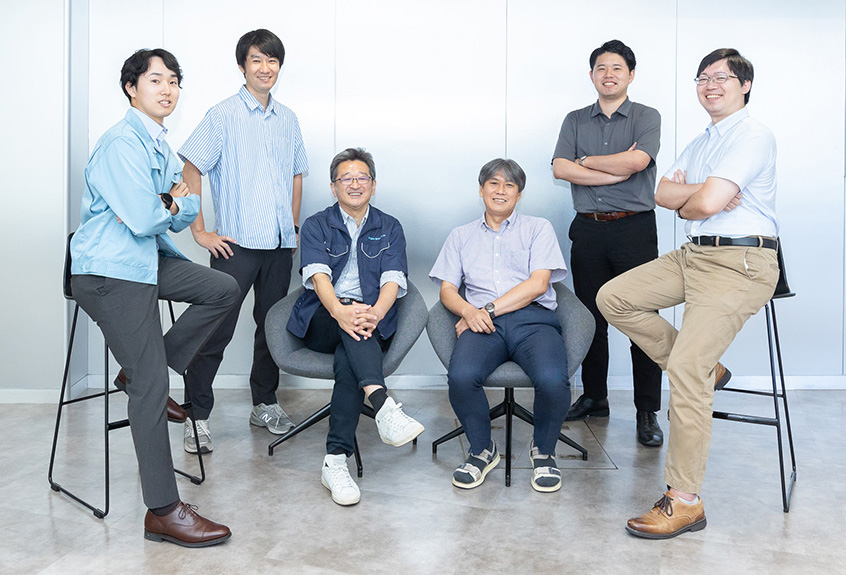
Related Links
- From the manufacturing of small parts to the assembly of large satellites: The dedication of team members on the front lines of monozukuri supporting space missions
- Space System: Solutions & Services | NEC
- Lockheed Martin and NEC to Enhance Satellites, Space Travel with Artificial Intelligence: Press Releases | NEC
- Satellite Equipment: Products | NEC Space Technologies, Ltd.