Global Site
Breadcrumb navigation
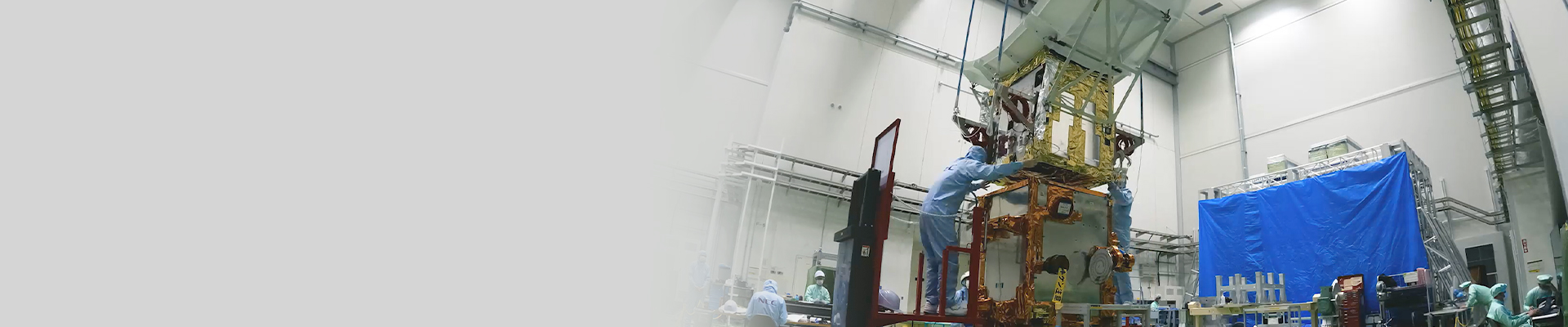
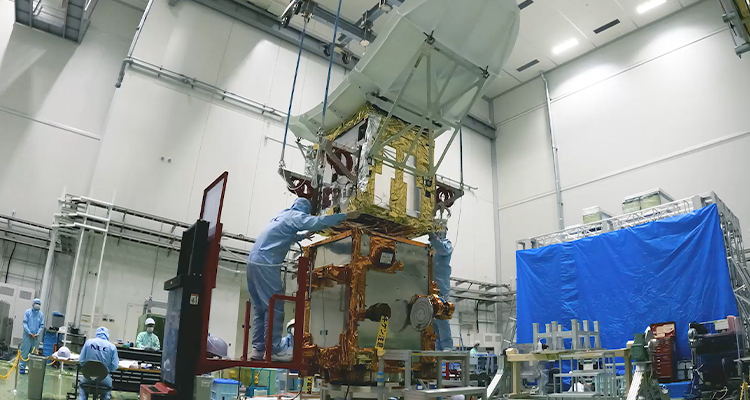
From the manufacturing of small parts to the assembly of large satellites: The dedication of team members on the front lines of monozukuri supporting space missions
Once a satellite is launched, it cannot be repaired. To endure the harsh environment of space—a near-vacuum environment with extreme temperature fluctuations—and successfully carry out missions over the years, robust monozukuri (i.e., the Japanese art of manufacturing) is crucial. What kind of monozukuri takes place at NEC, which handles the entire process from designing and manufacturing onboard equipment to satellite assembly, testing, and launch? We spoke with three employees about the dynamics on the front lines of satellite integration(*) and onboard equipment manufacturing.
(*) Satellite integration refers to combining various onboard devices to create a fully functioning satellite.
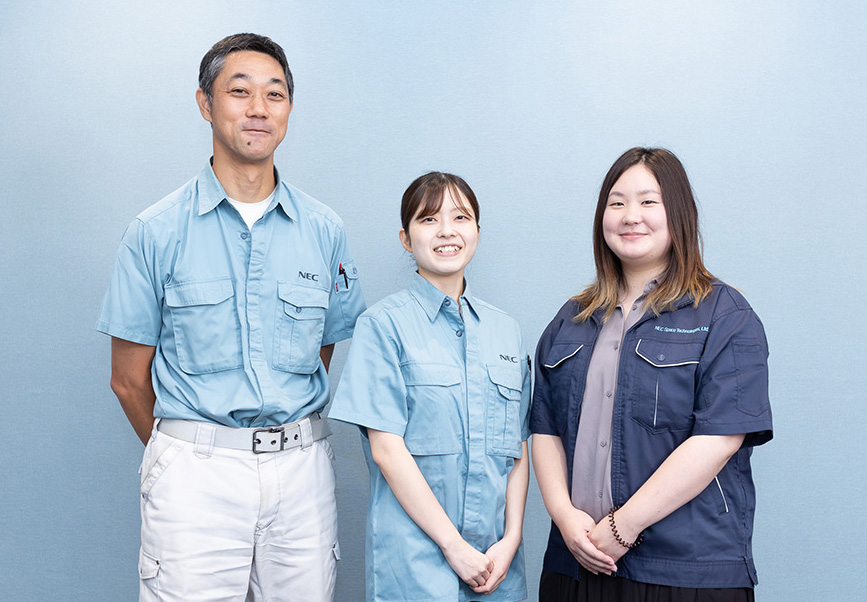
The NEC Group: A one-stop-shop for the manufacturing of diverse satellites
──Please tell us about your background and current job.
Shibasaki: I have been involved in satellite integration since I joined NEC in 1998. Back then, we carried out satellite assembly and testing at locations like JAXA’s Tsukuba Space Center, but since the Satellite Integration Center (a facility for satellite assembly and testing) opened at our Fuchu Plant in 2014, we have been handling everything in-house at the NEC Group’s facilities. I have worked on many satellites over the years, including Hayabusa2, ASNARO-2, and XRISM, and now oversee the manufacturing site with a focus on satellite systems.
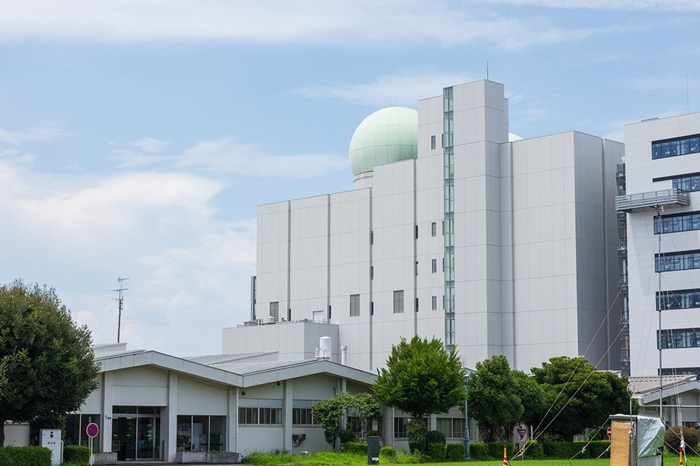
Soma: I joined NEC in 2019 and was assigned to the Aerospace National Security Business Unit. In my first year, I worked on manufacturing wire harnesses (bundles of cables that supply signals and power to onboard devices), and in my second year, I handled thermal instrumentation (attaching components to control the satellite’s temperature). Since 2021, I have been engaged in satellite integration.
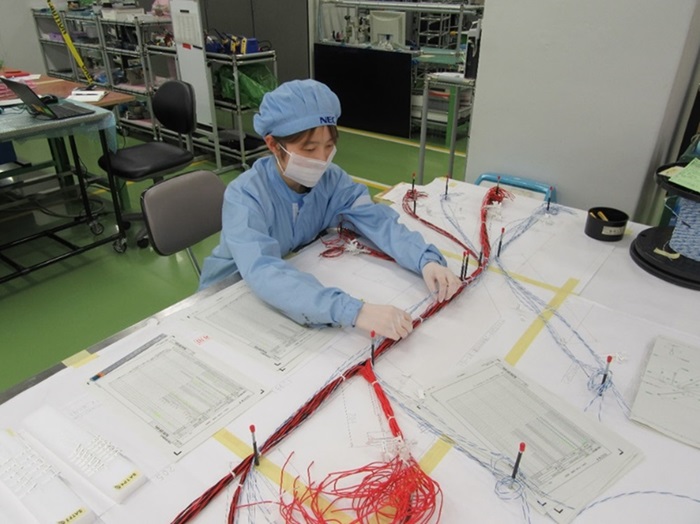
Uetake: I joined NEC Space Technologies in 2012, focusing on manufacturing RF (high-frequency wireless communications) equipment, such as passive devices, receivers, and transmitters, designed to observe electromagnetic waves from Earth and to be mounted on satellites.
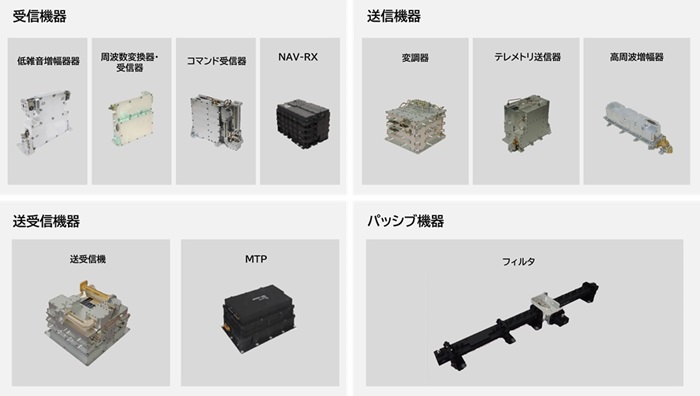
──Please give us an overview of the satellite development and manufacturing activities of the NEC Group.
Shibasaki: Satellites come in many forms, such as Earth observation satellites, communication satellites, and scientific satellites. The NEC Group handles all types. What sets us apart is our ability to develop and manufacture a wide range of satellites and our end-to-end capabilities—from designing and producing the main satellite and onboard equipment to testing them.
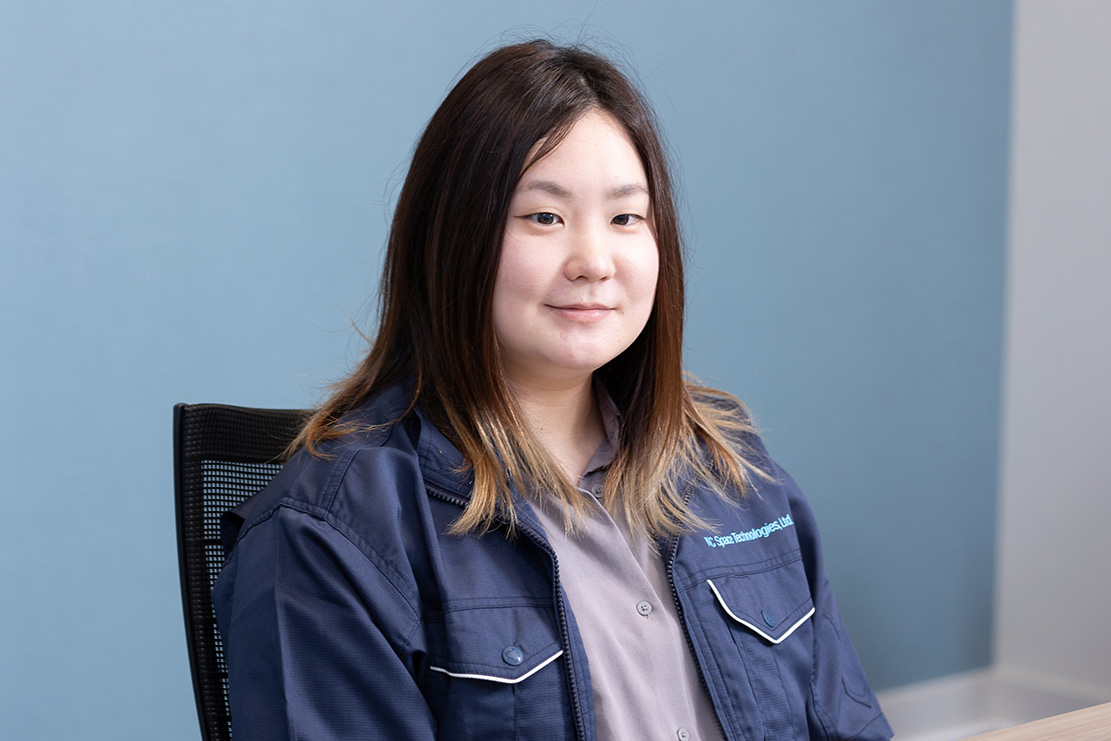
Uetake: NEC Space Technologies manufactures onboard equipment supporting a broad range of satellite subsystems, including communications, power, data processing, attitude control, and thermal control. We have manufactured over 9,400 onboard devices for various satellites other than those for NEC, with an installation track record of over 400 satellites across 30 countries.
──How do NEC and NEC Space Technologies collaborate on satellite production?
Shibasaki: The basic workflow involves NEC Space Technologies manufacturing the onboard devices, which NEC then attaches to the satellite’s structure, assembling it into a complete satellite. We do occasionally collaborate on subsystem testing, but overall, the manufacturing process is divided between us, and we rarely work on integration together at the same site. However, since we are all involved in satellite production, we know each other well.
Uetake: We handle a large number of parts for onboard equipment, and being involved with so many satellites and aspects of manufacturing is one of the biggest appeals of this job.
High-precision monozukuri driving the success of space missions
──Can you walk us through the process of integrating a satellite?
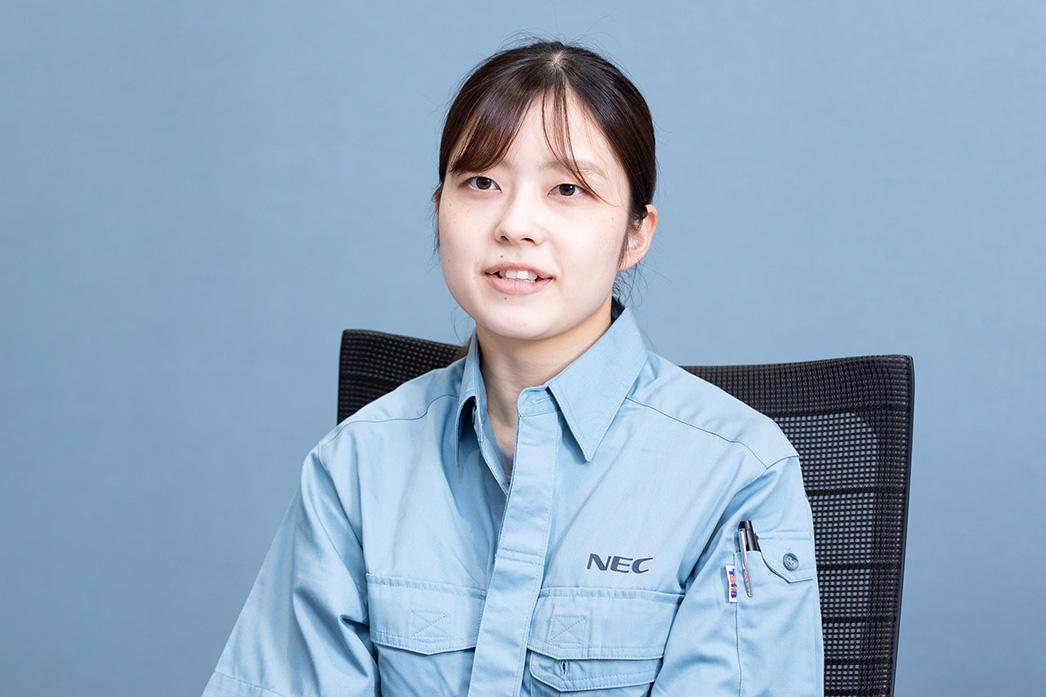
Soma: Each satellite is custom-made, with different designs and specifications. We start from the ground up for each satellite, including wire harness and thermal instrumentation designs, routing all cables by hand. We then integrate the onboard equipment from NEC Space Technologies into the satellite, conduct various tests, and finally transport it to JAXA’s Tanegashima Space Center or another launch site.
Shibasaki: For larger satellites, the installation of equipment often involves working in high places, so our Satellite Integration Center is equipped with multiple cranes and aerial work platforms. Both Soma-san and I have obtained the necessary qualifications, and we use these cranes and aerial work platforms for our tasks. Last year, Soma-san was also responsible for crane operations during a satellite’s installation onto a rocket at the Tanegashima launch site.
Soma: In addition to NEC’s personnel, there were many people at the launch site, including representatives from JAXA and other companies, so I was very nervous while operating the crane.
──It must be deeply emotional to see a satellite you assembled being launched. Reliable monozukuri is indeed essential for successful launches and mission execution in space. What do you keep in mind to ensure quality?
Shibasaki: Once a satellite is launched, repairs are not an option. We are therefore meticulous, down to the tightening of each single screw. To ensure quality, we need to fully understand the satellite’s characteristics, not just the technical drawings, as mission and usage requirements vary.
Soma: Since wire harnesses and thermal instrumentation cannot be replaced in space, we carefully perform every task, anticipating all possible scenarios. We also pay close attention to cable routing and placement to ensure they do not interfere with subsequent processes.
Uetake: Obviously, precision work is essential, and even something as basic as soldering needs to be done to a very high standard. Since satellite missions span several years, any equipment or part failures are unacceptable.
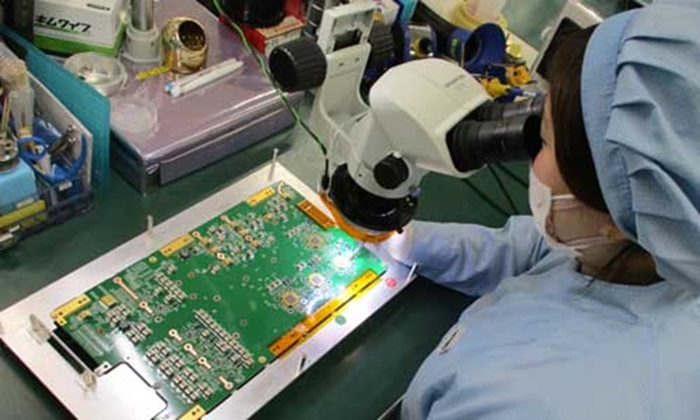
──It truly is a world of pure craftsmanship. NEC Space Technologies has even produced individuals recognized as Contemporary Master Craftsmen by the Ministry of Health, Labour, and Welfare. How are these skills cultivated and passed down?
Uetake: We currently have three Contemporary Master Craftsmen. To achieve their skill level, it is crucial to strictly comply with manufacturing standards. We refine our skills through technical training and by observing and learning from senior engineers during day-to-day operations, and not hesitating to ask for help when needed. Additionally, NEC Space Technologies launched the NEC Space Certified Master Program in 2024 to further enhance technical skills. One step in this program is the NEC Space Junior Master certification, for which I have been selected as a candidate. I am committed to honing my skills and mentoring the next generation.
Fighting daily against pressure: From precision work to installations at great heights
──Please tell us about the ingenuity involved and the key points you focus on in your daily work.
Soma: Satellite parts are all precision components and extremely valuable, so I concentrate intensely when installing them. Especially when working at great heights, I am particularly careful not to drop anything and make sure everything is well-protected to prevent any damage, just in case. So far, no accidents have occurred.
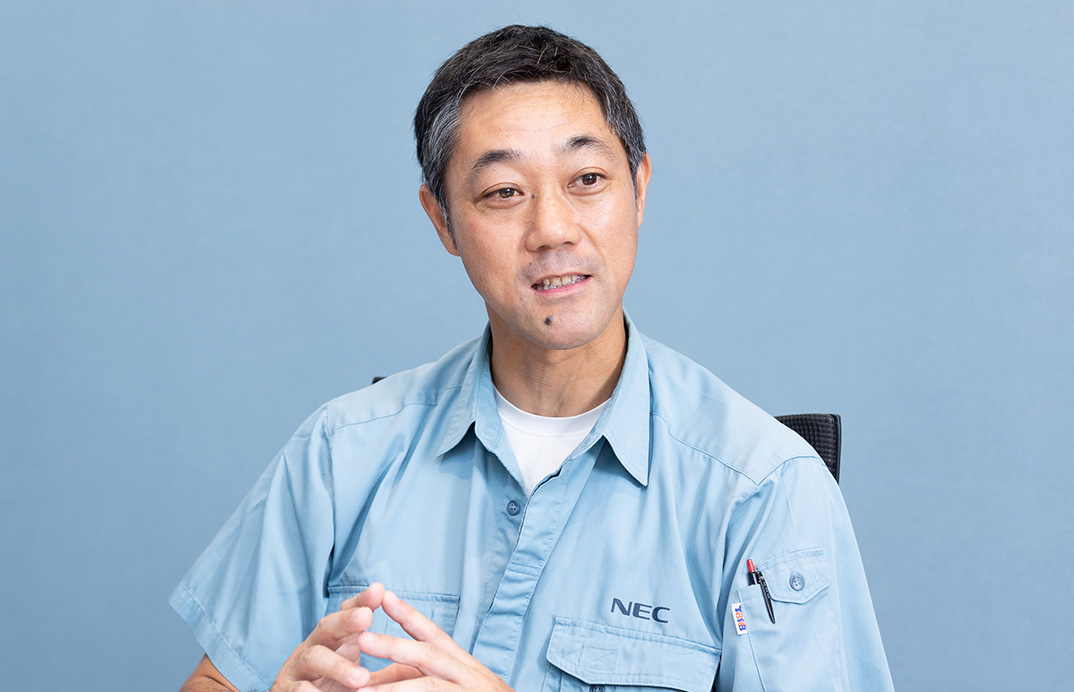
Shibasaki: Damaging any equipment or parts could delay a launch, so we cannot afford to make even the smallest mistakes.
Uetake: The same applies to the production of parts and equipment. If we do not adhere to the specifications and maintain millimeter-level accuracy, it will affect the subsequent processes. We try to work carefully, not only to avoid defects but also in consideration of the installation process and long-term durability in space.
Shibasaki: Since my current work focuses on overseeing the integration process, I am primarily engaged in schedule management and training of next-generation engineers. Nevertheless, monozukuri remains my field of work. That’s why I still make it a point to visit the Satellite Integration Center to check the situation regularly and occasionally demonstrate tasks to provide on-site guidance.
──Please tell us about the challenges and rewards of your work.
Soma: Working at great heights is always challenging and nerve-wracking. There are many times when we have to install equipment in awkward positions, especially when turning large screws, which requires significant strength and the ability to maintain a stable posture. We have to work carefully under constant pressure because “one slip, and it’s over,” but the responsibility it entails makes the job rewarding.
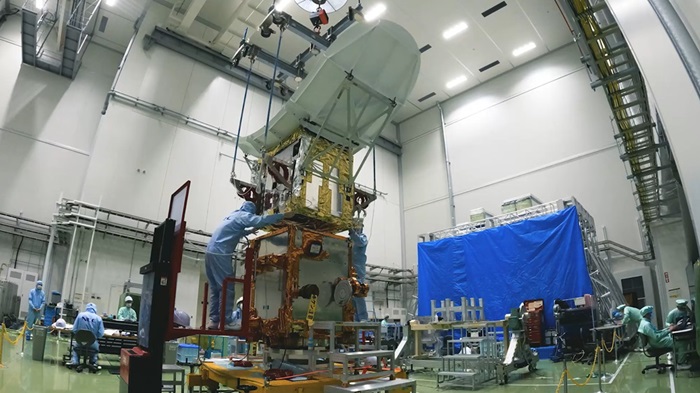
Uetake: With the advancement of technology, the parts, tools, and manufacturing methods we handle are constantly evolving. When taking on new tasks for the first time, we often have to go through trial and error. But when everything goes smoothly and we successfully pass the tests, the sense of accomplishment is even greater. It’s also incredibly satisfying to watch news segments on satellite launches and imagine the parts I made are on board.
Shibasaki: Our job is to integrate satellites in preparation for those launches. Managing schedules and overseeing the work can be challenging, but the anticipation of seeing the satellite take off into space is what keeps me motivated day in and day out. Thankfully, I have had the opportunity to be involved in nine launches so far. The joy does not just come at the moment of a successful launch. Hearing the post-launch reports, the media coverage, and receiving feedback from customers once the satellite is in orbit are also major sources of fulfillment for me.
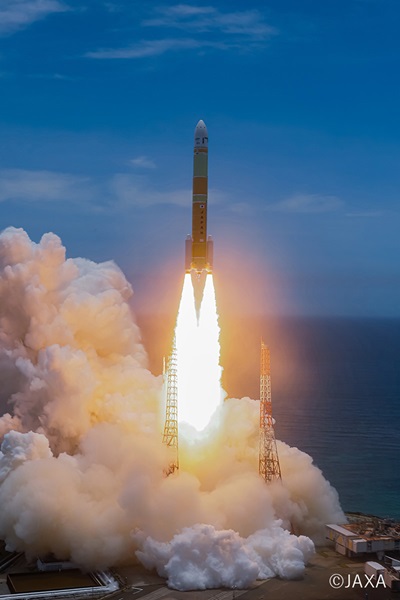
NEC and its role in spreading the word about the advancement of women in the space business
──Could you please tell us about the value your monozukuri efforts bring to society and your vision for the future?
Shibasaki: I believe we are extensively contributing to people’s daily lives by creating satellites and onboard equipment for various applications, including national security, scientific observation, earth observation, communications, and positioning. In particular, the success of the Hayabusa2 mission lifted spirits in Japan and brought excitement to the nation while also serving as an opportunity for many to learn about NEC’s space business.
Uetake: NEC Space Technologies manufactures an extensive lineup of satellite onboard equipment, with our telecommunications equipment being held in high regard worldwide. In that sense, you can say that our technologies are contributing to the development of the space business. Devices and parts like these are manufactured and delivered during the initial phase of a project. So by the time the satellite with them on board has been launched, we have already started our next round of monozukuri activities. Going forward, we will continue refining our technologies to create value for the future with satellites that have yet to take shape.
Soma: To engage in monozukuri that generates value, you also need the right skills and qualifications. Since various qualifications are required for satellite assembly and testing, I would like to be proactive in obtaining qualifications I don’t have yet, including Technical Radio Operator for On-The-Ground Services and Operations Chief of Hazardous Work of Oxygen Deficiency and Hydrogen Sulfide, to expand the scope of my work. Now that I am in my sixth year with the company, I am also aware of the importance of passing on my experience and knowledge to younger employees.
Shibasaki: Creating an environment where anyone can play an active role on the front lines regardless of gender is one form of value creation that only NEC can provide. While some were surprised to see Ms. Soma operating the crane at Tanegashima, I believe our mission is to make this a common sight. I hope to continue working to create opportunities for the advancement of women in the space business.
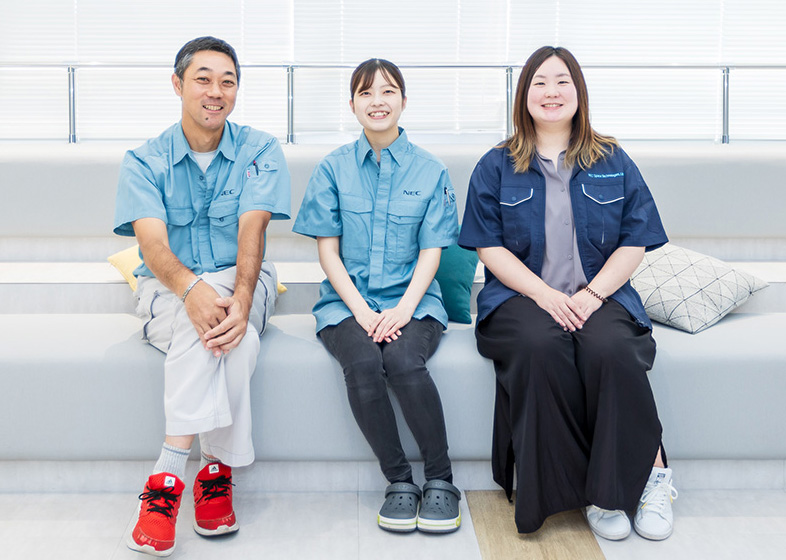