Global Site
Breadcrumb navigation
NeCycle®, a gorgeous and highly-functional cellulose-based biomaterial
Featured TechnologiesMarch 9, 2020
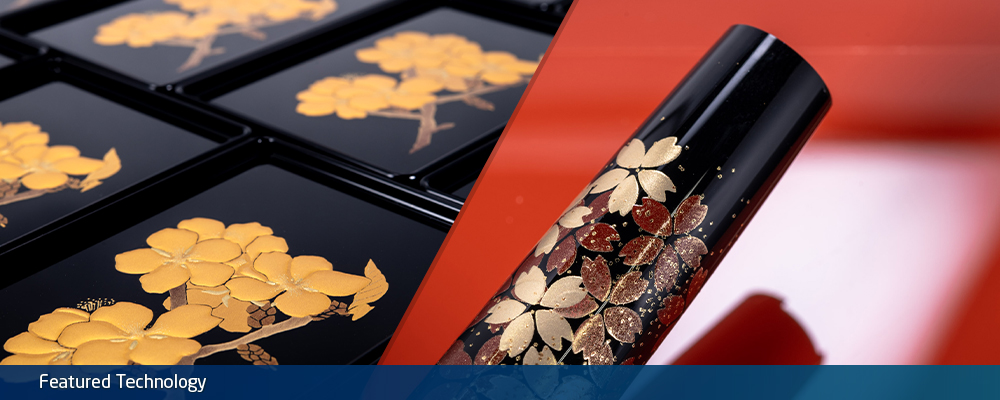
At present, plastic is used widely throughout the world due to its excellent moldability, heat resistance, and ease of mass production. However, plastic is a material derived from petroleum. That is why there are concerns that the fossil resources may run out in the future. Additionally, it has an adverse environmental impact on the natural environment because it is not biodegradable. The ocean plastic waste problem in particular has been garnering attention worldwide.
NEC has had a head start at attempting to tackle these problems with plastic, working on developing alternative materials since the early 2000s. One of NEC’s major accomplishments has been the successful creation of flame retardant and highly durable corn-based polylactic acid, a bioplastic which was starting to see increased use at the time. Polylactic acid is susceptible to heat, but adding natural materials such as kenaf and safe flame-resistant components found in soil has transformed it into a highly functional and durable material, making it possible for the material to be used in components found in cellphones, computers, and fuel dispensers. Since the 2010s, NEC has also been working on developing materials which use inedible plants because of the expected future problems of population increase and food shortages. NEC has been developing original resins made from cellulose which is extracted from wood and straw. The development of materials which have both high bio-based content and high functionality are things which NEC has continued to working on independently. NeCycle®, the highly-functional cellulose-based biomaterial which we will be covering today, is a new material that has been developed as a result of that research. We spoke with the researchers about the details.
A new freely moldable material resembling gorgeous black lacquerware
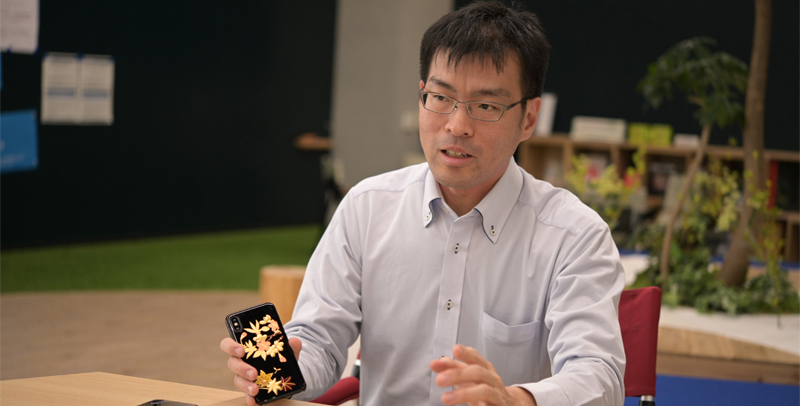
Research Manager
System Platform Research Laboratories
― What kind of material is the NeCycle® highly-functional cellulose-based biomaterial?
Tanaka: It’s a biomaterial that is composed of approximately 50% inedible cellulose, but is similar enough to resin in terms of its properties to be used in electronics. I don’t think there’s any other material which contains such a high concentration of inedible plant-based materials while also maintaining the properties of resin to such a degree. I’d also like to bring your attention to how highly decorative it can be. It has a deep and warm blackness that is akin to that of lacquerware. The main characteristic of this material is that it can be freely molded and achieves this gorgeous blackness like lacquerware without any coating process. It can be manufactured by injection molding just like regular plastics. It does not need coating process unlike synthetic lacquerware (plastics coated with lacquer), so the shapes that can be formed and the ability to mass produce should be greatly increased. Aside from the obvious reduced negative environmental impact, it’s an entirely new kind of material that makes it possible give components of various shapes an air of luxury thanks to its black lacquerware-like appearance.
Toyama: In order to make this blackness possible, we sought cooperation and worked together with one of Japan’s leading Japanese lacquerware artists, Dr. Yutaro Shimode (third-generation president of the Shimode makie-studio and professor of the Faculty of Cultural Studies at Kyoto Sangyo University). Getting an opportunity to work together with him is difficult because he’s a very renowned artist, but he agreed to work with us because he identified with our desire to popularize biomaterials throughout the world.
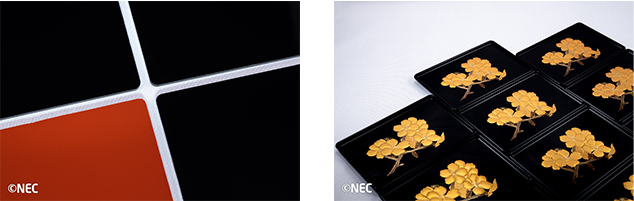
― What made you decide to focus on the black found in Japanese lacquerware?
Tanaka: Compared to existing mass producible materials such as petroleum-based plastics, biomaterials end up being less cost-effective. Therefore, we thought it would be necessary for it to have further value of some kind in order for it to see widespread use in the marketplace. Our team, including Toyama, then conducted some domestic and overseas market research and that’s when we found out that the beauty of Japanese lacquerware is highly regarded worldwide. We decided that the beauty of Japanese lacquerware could add enough value to help overcome the cost barrier, and that’s why we took on the challenge.
If we can use the NeCycle® to help spread the idea that biomaterials can be used in various ways, then it should lead to a stable increase in production. As the amount increases, the costs will go down, eventually reaching the point where it should be able to compete with existing plastics. I’m really hoping we can further accelerate the process of making this material functional so that that becomes a reality.
A deep and warm blackness acknowledged by a Japanese lacquerware artist
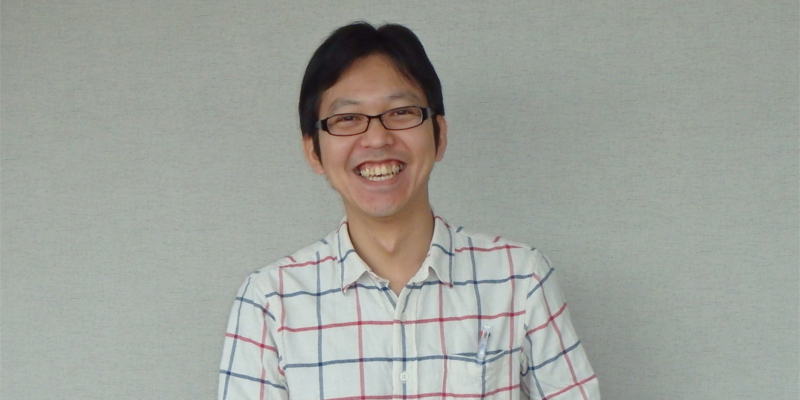
Principal Creator
System Platform Research Laboratories
― How did you go about making this deep black hue possible?
Toyama: We started out by having Dr. Shimode make some Japanese lacquerware to serve as a model so that we could have as clear a target as possible to aim for. Our first step was to analyze and quantify the luster and shade of black of that model. We then conducted many experiments in an attempt to create something with similar values, but the number of possible combinations of colorants and amounts made things practically infinite. We used our knowledge to continue the trial and error process in an attempt to create something similar to our model. Ever since NEC began work on flame-retardant polylactic acids, the company has continued to improve on its original compounding technology which improves the functionality of a base resin by adding various components. This reservoir of expertise is one of the factors which helped lead to the successful creation of this material.
However, we’re talking about a shade of black which has taken a traditional craft countless years to develop, so there were aspects which couldn’t be expressed through numbers alone. That’s why we had the doctor check our prototypes over and over as we continued the development process. Our initial prototype wasn’t rated very highly, but we used the feedback we received to create more prototypes until our final product received high ratings. I believe that the NeCycle® doesn’t just resemble our model numerically, it also manages to capture the unquantifiable properties of depth and warmth unique to Japanese lacquerware.
Tanaka: I feel like this black hue might have been a good fit for the cellulose resin which we used as a base for this material. The reason I say this is because the black hue found in Japanese lacquer is made by mixing semi-transparent yellowish sap with iron. Our cellulose resin uses wood and straw as a base, and it’s also originally a somewhat semi-transparent yellowish kind of resin. And since we add black colorant to it, that might be what has made it possible to express the deep blackness of lacquerware. This depth is something which might not be possible with transparent petroleum-based resin.
Toyama: However, upon hearing how shiny and black this is, some people may be concerned that scratches will be easily visible. Actually, right after we announced our prototype, we received such concerns from multiple individuals. In response, we’ve currently added additional components to improve the material’s anti-friction properties. It was a very difficult challenge to improve the material’s functionality while preserving its unique black hue, but the result is a material with better anti-friction than materials such as acrylic and ABS resin.
Tanaka: For those who are inclined to create something like real Japanese lacquerware, it’s even possible to recreate maki-e (a traditional picture drawn with a brush on the surface of lacquerware). We conducted some collaborative research with a printing company and were able to print a three-dimensional copy of an elaborate maki-e. Since it’s recreated via printing, that makes it possible to mass produce.
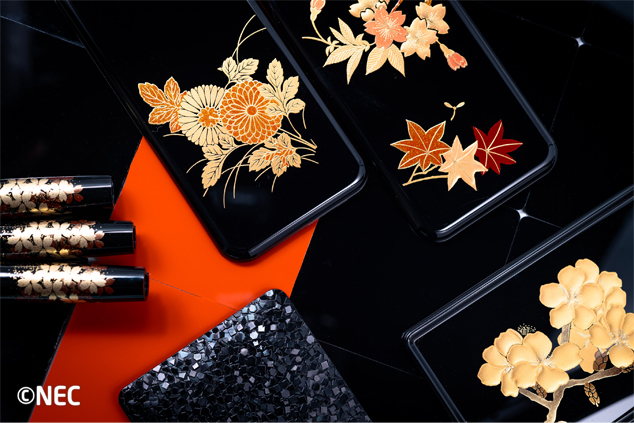
Expanding the areas where biomaterials see use
― What kind of applications do you think are possible?
Tanaka: We foresee the material being used in high-end products in general such as luxury everyday items like wristwatches and fountain pens, high-end household appliances, building materials, and home and car decorations. Before that can happen however, we believe it will be necessary to improve the material’s durability and heat resistance, so we’re continuing research to further enhance the material.
Toyama: We’re working on improving the material from two angles; the first is by adding more components to enhance its functionality, the second is by improving the cellulose resin base which we use. We already have an idea of how to achieve these things, so we should be able to further improve the NeCycle® through continued research.
Tanaka: One of our future primary goals is to use this material as a catalyst to expand the uses of biomaterials in order to help society move towards a circular economy. We don’t think this material alone is enough to achieve that, so we hope to develop and increase the variety of biomaterials so that there’ll be a right biomaterial for the right job.
Toyama: I agree. Environmental issues have recently been gaining attention once again, so when I’m conducting research to develop new materials which don’t interfere with the earth’s environment, I feel like it’s very important and meaningful. I hope to be able to continue focusing on the development of new biomaterials which will see use in an even wider array of areas.
Tanaka: In fact, ever since the press release about the NeCycle®, I’ve had the opportunity to speak with customers from various industries. It made me realize just how varied the views and needs can be when it comes to biomaterials depending on the industry and intended use. This firsthand information on these kinds of needs and wants is actually something we’ve wanted the most. Now that we better understand what people from various industries other than electronics which NEC produces want from our material, it’s really expanded the directions we can take our research. We hope to use the valuable feedback we’ve received from our customers to develop new materials which can be in harmony with the environment and also pave the way for society to move towards a circular economy.
- *Part of this research was conducted with the assistance of the JST ALCA.
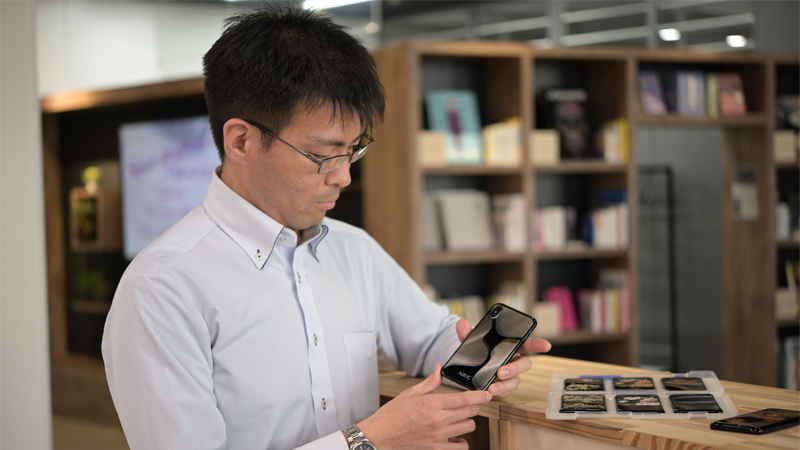
- ※The information posted on this page is the information at the time of publication.