Global Site
Breadcrumb navigation
Space ship carrying humanity’s 100-year dream
IKAROS was developed to demonstrate a Solar Sail which gathers sunlight as propulsion and a Solar “Power” Sail which gets electricity from thin film solar cells on the membrane.
The sail of the IKAROS opens a huge square some 20 meters in a diagonal line by the centrifugal force of spinning the main body of the IKAROS and generates enough energy from sunlight with thin film solar cells.
Also, IKAROS has a navigation technology using the solar sail by controlling the orbit by adjusting the direction of the sail.
This is a historical world-first achievement.
IKAROS was launched on May 21, 2010 with H-IIA 17 launch vehicle.
Sailing into Space: Two men in a race against time
Project manager: Masahiro Umesato, NEC Corporation
Electrical systems engineer: Takakazu Okahashi, NEC Aerospace Systems
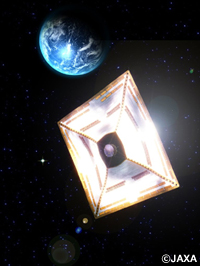
Launched at the same time as the Venus Climate Orbiter Akatsuki, IKAROS (Interplanetary Kite-craft Accelerated by Radiation Of the Sun) is the world's first solar power sail craft, propelled through space by converting the sunlight reflecting off an ultra-light 200 m² sail. IKAROS does not use rocket propellants—but instead uses the power of sunlight, continuing to accelerate, in theory, forever. The push from the sunlight is very slight, and so too is IKAROS's acceleration. However, if IKAROS continues to accelerate for many years, it might travel faster even than a spacecraft propelled by rocket engines.
The realization of the solar power sail concept depended on the deployment of an ultra-light thin membrane in space. However, although the basic idea of solar-powered momentum had been figured out more than a century ago, nobody had deployed a solar power sail in space. In the last ten years, several attempts were made to launch an experimental solar power sail craft, but these did not succeed. IKAROS is therefore the world's first spacecraft to successfully demonstrate solar power sail technology, fulfilling a century-old ambition.
It usually takes at least five years to develop a scientific satellite or probe. This is because a new sensor and satellite has to be developed for each different observation target. However, IKAROS was launched just two and a half years after the start of development. Moreover, it cost ten times less than usual.
Two engineers at NEC took on the challenge of developing this unprecedented experimental spacecraft under such severe conditions.
Matsuura: From deployment of the solar power sail to confirmation of acceleration based on solar light and attitude control using the sail, you have succeeded almost one hundred percent with IKAROS. Until the IKAROS project, what kind of satellites had you been developing?
Umesato: I joined NEC in 1980, and was mainly involved in developing satellites such as the broadcast satellite Yuri-3, the advanced land observing satellite Daichi, and the super high-speed Internet satellite Kizuna. IKAROS was my first project as project manager. I say project manager, but the IKAROS project really had a very small team, consisting of just two members, Mr. Okahashi and myself. I was in charge of the mechanical systems while working as the project manager and systems manager, and Mr. Okahashi was in charge of the electrical systems.
Okahashi: I was involved in developing the lunar probe LUNAR-A, whose development was abandoned. It was very hard for me to have a project that I had worked on for so long be abandoned. However, 2010 was a much better year, with the safe return of Hayabusa's re-entry capsule—I was in charge of developing it—and the success of IKAROS.
Matsuura: What parts of IKAROS was your team responsible for developing?
Umesato: The solar power sail on IKAROS—that part to be deployed in space—was built by JAXA. We were responsible for developing and building the probe's main body, which is the cylindrical part in the center of the satellite. This cylindrical main body formed the hub to which the sails and the sail deployment mechanism were attached, and included communication devices, attitude sensors, thrusters for controlling the attitude and rotation, and other vital equipment. We developed the overall systems, which were then designed in detail by NEC's design department and built on NEC's manufacturing lines.
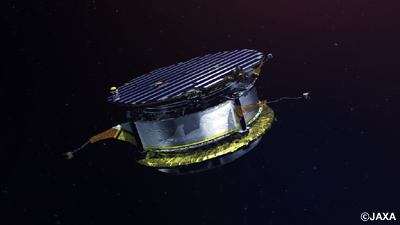
Before IKAROS's sail deployed
The cylinder in the center is the probe's main body, and the part on the top is the solar cell array.
Here, IKAROS is just starting to deploy its sail.
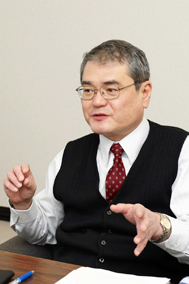
Matsuura: Even so, two people seems like an awfully small project team.
Umesato: The IKAROS project happened very quickly. The Venus Climate Orbiter Akatsuki was initially designed to be launched from an M-V rocket, but suddenly the M-V line was discontinued, and the decision was made to launch Akatsuki from an H-IIA rocket instead. Then, while we were analyzing Akatsuki's H-IIA rocket launch simulation, we discovered that Akatsuki was too light, causing the rocket to vibrate excessively during second-stage acceleration. The only way to suppress this acceleration was to add a 700 kg dummy payload*1 to the 500 kg Akatsuki. But of course we realized that it would be a waste to send 700 kg of nothing all the way to Venus, so we started to think about how we could effectively utilize the launch of Akatsuki. And that's how the IKAROS project was born. The person who proposed this project was Professor Junichiro Kawaguchi of JAXA, who supervised the development and operation of the Hayabusa asteroid probe. I heard that after seeing the Akatsuki project's vibration analysis results, Professor Kawaguchi went away and came back one week later with a proposal. He really singlehandedly launched the IKAROS project.
More than ten years earlier, Professor Kawaguchi had proposed exploring the Jupiter and the Trojan asteroids by using a probe that combined an ion engine and a solar power sail. So the first thing the professor did to prepare for this mission was develop a device to demonstrate solar power sail technology.
- *1 Dummy payload: When launching an experimental spacecraft, it is sometimes necessary to attach a weight to the launch rocket to balance the weight or size of the actual satellite. This weight is known as a dummy payload. In the case of the Akatsuki launch, a weight equivalent to IKAROS needed to be added to suppress vibration.
Okahashi: Because the project happened so quickly, there was basically no time or money available. We were assigned a budget of 1.5 billion yen, and a development period of two and a half years.
Umesato: With such a small budget, we could not afford a large team. It was decided, therefore, to have just two full-time project members. The two and a half year development deadline was also extremely tight—almost impossible really.
The focus of the launch was the Venus Climate Orbiter Akatsuki, so the launch date was fixed based on the position of Earth and Venus. Which meant that the launch would take place whether IKAROS was ready or not. We knew this at the beginning. It might have been easier if we knew that even if IKAROS couldn't be launched with Akatsuki, we could at least complete it, but this wasn't the case. Akatsuki needed a dummy payload, and as we hadn't prepared anything else, IKAROS would have to be launched even if it wasn't complete.
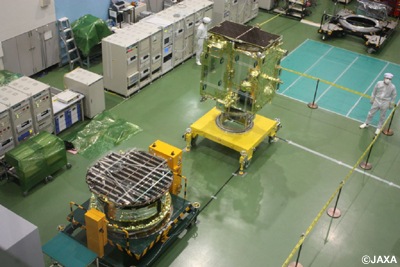
and the compact solar power sail demonstrator IKAROS (front) undergoing testing
Matsuura: So with no money and no time, and knowing that you only had one chance to launch it, how did you succeed in completing IKAROS?
Okahashi: We realized that we would only be able to stay on schedule and keep costs down if we procured as many parts as possible from other sources.
Matsuura: What do you mean?
Okahashi: I mean that we took parts from other satellites such as the lunar probe LUNAR-A, whose development had been abandoned before launch. The LUNAR-A main body was complete, but its penetrator, an observation device, was proving troublesome to develop. We also used LUNAR-A's battery, solar sensor, which is used to determine the attitude, nutation damper*2 for spin stabilization, and thruster valves. We also procured the power regulator from the ground test model of Hayabusa. The power regulator is used to keep the power obtained from the solar cell at a constant level.
- *2 Nutation damper: When a spinning top slows down, its rotational axis starts to wobble. This kind of wobble is called nutation. If nutation occurs when a satellite spins in space, it might cause a malfunction. A nutation damper is therefore used to stabilize the spin of the satellite. A nutation damper consists of a cylindrical pipe filled with liquid. Nutation causes the liquid to shake, and the nutation energy generated by the friction between the liquid and the pipe is converted into heat energy, which suppresses the shaking.
Umesato: The communication device did not have to be designed afresh because we could use the same device as the one mounted on Akatsuki. We simply got the manufacturing department to make a device based on the same design. This really helped lower our design costs.
Matsuura: Did IKAROS present any particular challenges in terms of design?
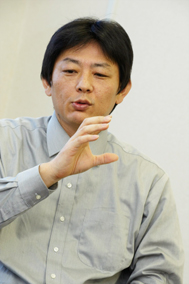
Okahashi: The basic configuration of IKAROS was based on the concept of rotating the main body and stabilizing the spin in order to stabilize the attitude. This kind of configuration is simple, and technically easy to build. So in terms of the basic design, we didn't have any major concerns.
Umesato: The solar power sail caused some headaches because an error of even one millimeter in its position would change the equilibrium of the main body, making it difficult to determine where to place the devices. Pre-launch analysis results showed that the slightest shift in equilibrium away from the sail would cause the main body to flip over when the sail deployed.
Okahashi: The sail created some heavy constraints.
Umesato: When developing a satellite or probe, prior to manufacturing the actual device, we usually create a structural thermal model (STM), which is a test model that has the same thermal conditions and strength as a mechanical test model (MTM) and thermal test model (TTM). The STM is then subject to thermal environment testing using a vacuum chamber to check whether the thermal conditions of the satellite or probe in space accord with the design. With IKAROS, however, we did not create an STM; instead we simply conducted a thermal vacuum test*3 on the actual launch module. I must add that we did create a mechanical test model with the same strength and rigidity as the actual device because we had to check the mechanical conditions of the incorporated devices before launch.
- *3 Thermal vacuum test: This is a test used to check the functionality of the devices incorporated in a satellite under the severe environmental conditions of space, such as a vacuum or high temperatures caused by solar radiation. The equipment used to recreate an environment similar to space is called a vacuum chamber.
Okahashi: The thermal vacuum test was very difficult, wasn't it? We had to work double shifts.
Umesato: Yes. The thermal vacuum test involved keeping the satellite in a thermal chamber for two weeks, but we had to observe the satellite for the whole time. And of course there were only the two of us. That was really hard…
Okahashi: The schedule became really tight from about one year prior to launch. Usually, we perform compatibility tests to check for any problems occurring between devices, and then general tests on the assembled satellite. These tests normally take up to a year to complete. But in our case, we just couldn't find the time to do compatibility tests. This meant that we had to carry out the compatibility tests as part of the general tests on the assembled satellite. It was the only way to stay on schedule.
Umesato: We were told by the ISAS to include a three-month margin in the schedule, which, somehow, we managed to do.
Accepting the risks, we just kept moving forward. This is absolutely not the way we normally go about developing a satellite! Once any risk becomes apparent, we normally stop, perform thorough testing, and confirm safety before continuing. If I was told to make IKAROS again, I guess I could because I now have this experience. But if I was told to make a new IKAROS from scratch under such severe conditions…well that would be very hard.
Matsuura: What kind of risks were involved in developing IKAROS?
Okahashi: The IKAROS sail membrane was equipped with thin-film solar cells and a dust counter. Even if these devices output abnormal values during testing, the sail membrane had already been folded, and couldn't be unfolded at that point because once unfolded, it is very difficult—and time consuming—to fold up again.
In fact, noise was detected on the signal output from the dust counter during the test. Of course normally we would take the time to find the cause of the noise and even delay the launch if necessary. But in this case, we evaluated the test results and assumed that the noise probably occurred outside the demonstrator and would not occur in space, and that the minimum required missions could be achieved by raising the detection level. We consulted with the principal investigators, asking if our assumption was reasonable, and they agreed that we should move ahead with development, giving the schedule first priority. The judgment was solid, but there remained a risk that the in-orbit performance might be limited. I have to say that I was very relieved in the end when the dust counter did not output noise after launch.
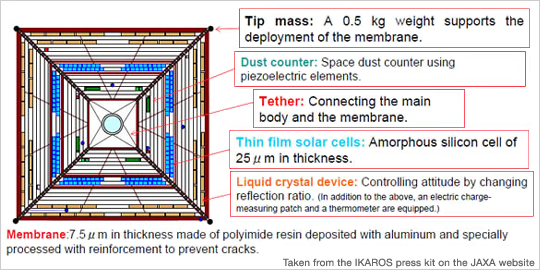
Umesato: Nevertheless, I really think that Mr. Okahashi carried out his development very carefully. One of the principle investigators at JAXA told me that Mr. Okahashi was very much a "better safe than sorry" type (laughs).
Okahashi: Well, I suppose that comes from my experience with LUNAR-A, which didn't make it to launch. That was quite a depressing experience for me. That's why I wanted to be as careful as possible, even though we didn't have much time. At the same time, however, I was always worried about not finishing in time for the launch. I really wanted IKAROS to be launched, and to succeed!
Matsuura: Was there anything about IKAROS that turned out easier than other development projects?
Umesato: There wasn't too much pressure to reduce the weight. IKAROS needed to weigh between 300 and 315 kg. But of course we had to be careful not to exceed the weight limitations when adding the balance weight at the end.
Matsuura: How did you feel about IKAROS's performance after launch?
Umesato: To be honest, I really didn't expect IKAROS to perform so well. I was convinced that there would be problems somewhere along the line. I think now, for the first time, I really understand the feeling of "complete success".
Okahashi: At the time, I thought there was probably about a fifty-fifty chance of the sail actually deploying.
Umesato: The deployable camera also worked well, didn't it? Being able to take photographs of the whole satellite in deep space like that—it was a world-first achievement. I confess that, during development, I did wonder why we were attaching these things (laughs). But the cameras did take really great pictures.
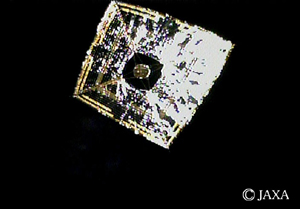
Okahashi: I was amazed when I first saw that photograph of the deployed sail. It was stunning.
Umesato: The IKAROS project really succeeded thanks to the tireless work of Mr. Osamu Mori, the project manager, and his team at JAXA. It was a superb group effort. Professor Kawaguchi oversaw the whole project and gave us support at critical points. He also attended most of the design meetings. I think for Professor Kawaguchi, the success of IKAROS was a kind of lucky break. He even said to me that this was a once-in-a-lifetime project. His were really words to live by.
Okahashi: At 300 kg, IKAROS can't really be called small. The size of the satellite is not necessarily related to the length of the development period, but this project taught me that, with a little creative thinking, a satellite really can be developed in as little as two and a half years. I think my experience with IKAROS will help me speed up my work when I next develop a probe.
When asked what he wanted to work on next, Mr. Umesato said that, since IKAROS was only a demonstrator, he would like to be involved in producing a real solar power sail craft—one that combined the ion engines that were successfully used in Hayabusa and the solar power sail used on IKAROS—with its own mission to explore Jupiter or the Trojan asteroids.
Technology is used to perform scientific observations—in fact, scientific observation is not possible without technology. IKAROS has demonstrated a new technology that can be used to perform scientific observations in space. IKAROS has surely paved the way for a journey to Jupiter or the Trojan asteroids.
Researched and written by Shinya Matsuura, November 30, 2010
Mission accomplished: IKAROS passes Venus
At 7:39 on December 8 (UTC), 2010—one and a half days later than Akatsuki—IKAROS passed by Venus at a distance of 80,000 km from the planet surface, travelling at a speed of 3.5 kilometers per second. The gravitational pull of Venus extends 600,000 kilometers, so IKAROS can be said to have completed an impressive Venus swing-by. As IKAROS gradually accelerated, its aphelion point (farthest point from the sun) moved outside Earth's orbit. At this point, the mission initially conceived for IKAROS was complete. (It achieved a full success level.)
On December 7th, Akatsuki failed to enter Venus's orbit, instead passing inside. Executing a powered swing-by using rocket engine propulsion, Akatsuki entered an orbit that is slightly shorter than Venus's, and that differs from the orbit of IKAROS.
As the first satellite in the world to successfully demonstrate solar power sail technology, the journey of IKAROS is far from over.
All eyes are now on IKAROS! (January 5, 2011)
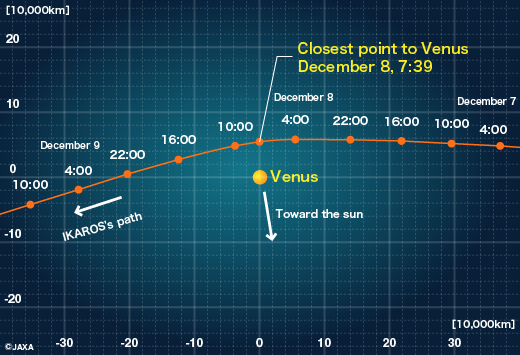
The orbit of IKAROS with reference to Venus
This graph shows the orbital position of IKAROS at 6-hour intervals
(based on the equatorial coordinate system (J2000.0) with reference to Venus, in units of 10,000 km)
The orbit of Akatsuki at its closest point to Venus passes inside Venus's orbit (toward the sun),
whereas IKAROS passes outside it.
Masahiro Umesato
Engineering Manager of the Space and Satellite Systems Department,
Space Systems Division, NEC Corporation
Joined the company in 1980. He has been involved in a range of projects related to scientific satellites, such as developing the structure of the Ginga satellite's main body and solar cell panel. He was also part of the team tasked with designing the mechanical system of Yuri-3 launched in 1991. He became the system design manager for Daichi in 1997, and for Kizuna in 2003. He is currently project manager of the IKAROS project, a position to which he was appointed in 2008.
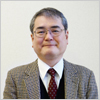
Takakazu Okahashi
Assistant Manager of the 1st Engineering Department,
Space Systems and Public Information Systems Division,
NEC Aerospace Systems
Joined the company in 1988. He was involved in developing the scientific satellite LUNAR-A, and in 2000 he started working on developing the Hayabusa capsule. He was subsequently appointed the systems manager of the Hayabusa project, becoming responsible for Hayabusa's systems, including integration and testing, right up to the launch. He also joined the Michibiki project, in which he was in charge of the mission systems for the positioning system (Quasi-Zenith satellite system). He is currently systems manager of the IKAROS project, a position to which he was appointed in 2008.
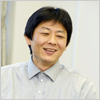